Closing the gap: How Archer Western and DroneDeploy observed a 1.1% difference in stockpile quantities vs traditional survey methods
Assessing stockpile levels is crucial for proper supply chain management. By knowing how much material is present on site, surveyors and GCs can optimize production schedules while reducing storage costs.
And because stockpiles fluctuate due to several factors — extraction, compaction, exposure to natural elements — ensuring accuracy depends on consistently reliable volume measurements, even as materials fluctuate.
Pablo Giraldo knows this better than anyone. In his role as Construction Technology Manager, he prioritizes the use of reality capture technology for Archer Western.
And when he needed to validate the precision of one of his stockpiles, he worked with Solutions Engineer Trevor Broussard to develop a high-accuracy workflow that compared volume measurements obtained from conventional surveying methods with DroneDeploy’s volume annotation.
The pile
Pablo and his survey team were tasked with documenting a stockpile at Big Creek, a wastewater treatment facility near Atlanta, Georgia.
The pile itself was 0.34 acres in area with a maximum vertical height of 10.08 feet, and composed of different types of excavated material.
The process
Over 45 minutes, the team used a robotic total station and rover to collect 65 data points – 33 points around the base of the pile and 32 points around the varying elevations surrounding its crest.
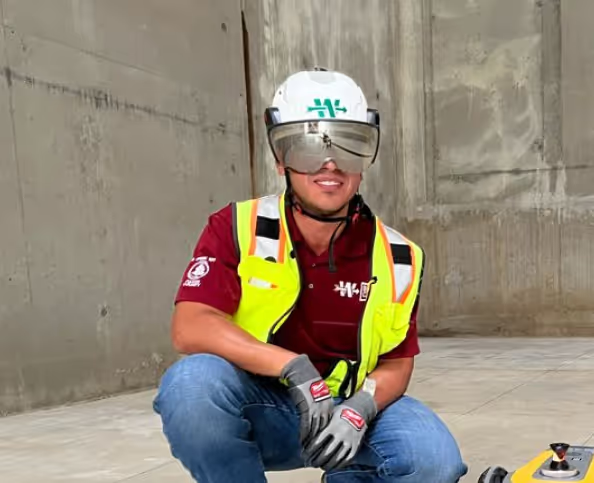
Collecting these points required setting up over a known point and projecting that location to an area closer to the pile. To do so, ten UAV aerial targets were laid out on and around the pile and precise locations were surveyed.
Seven of these points were chosen to be processed as ground control points to assist with georeferencing the map, while three were used as checkpoints to validate map accuracy.
The area was flown at 200 feet above ground level using DroneDeploy’s Terrain Awareness capability, which enhances map quality across diverse terrains, ensuring uniform resolution and minimizing the occurrence of gaps at higher elevations across diverse terrain.
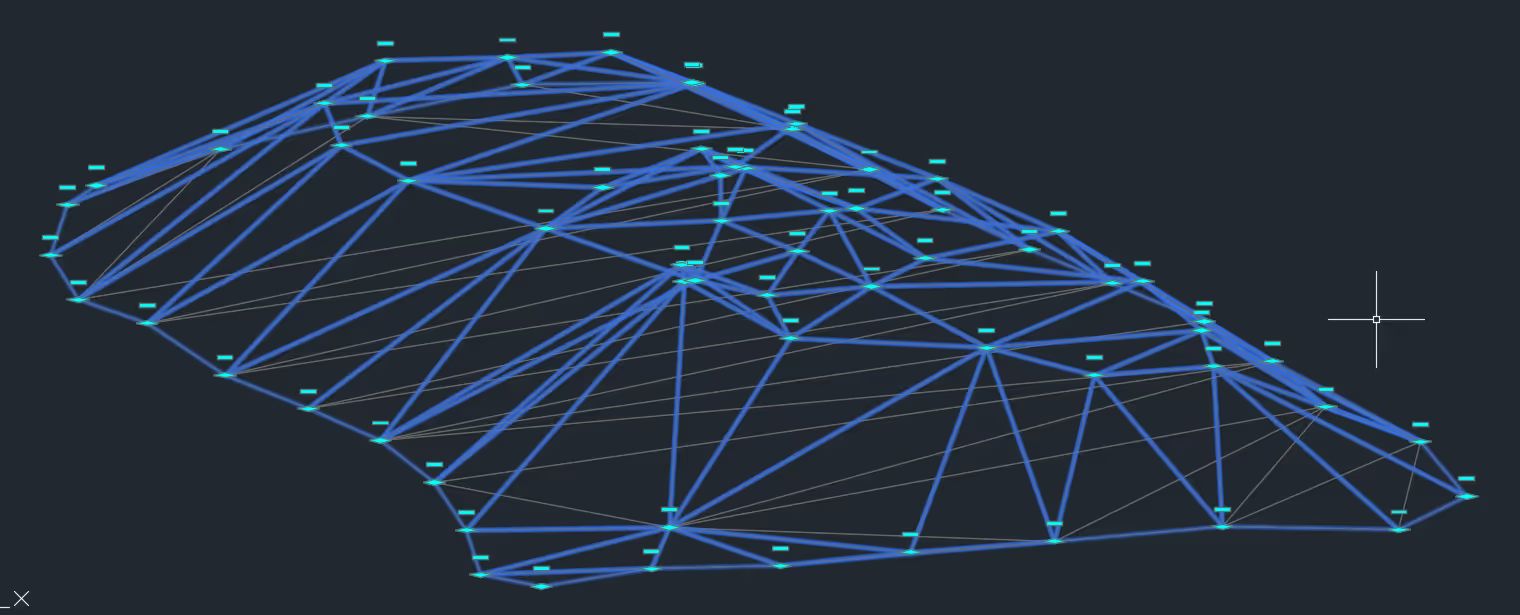
Tripling up imagery
In order to get a complete picture of the stockpile, the Archer Western team overlaid multiple reality capture methods over a single flight pattern. Instead of using direct points from the survey, the team developed overlapping geotagged photos into an integrated data model.
Using DroneDeploy’s flight planning tool, all map missions were pre-planned from a computer that triplicated the planned mission to account for different image types: oblique, nadir, and a combination of both. DroneDeploy’s Crosshatch 3D mode captured oblique imagery at a gimbal angle consistently at -65 degrees.
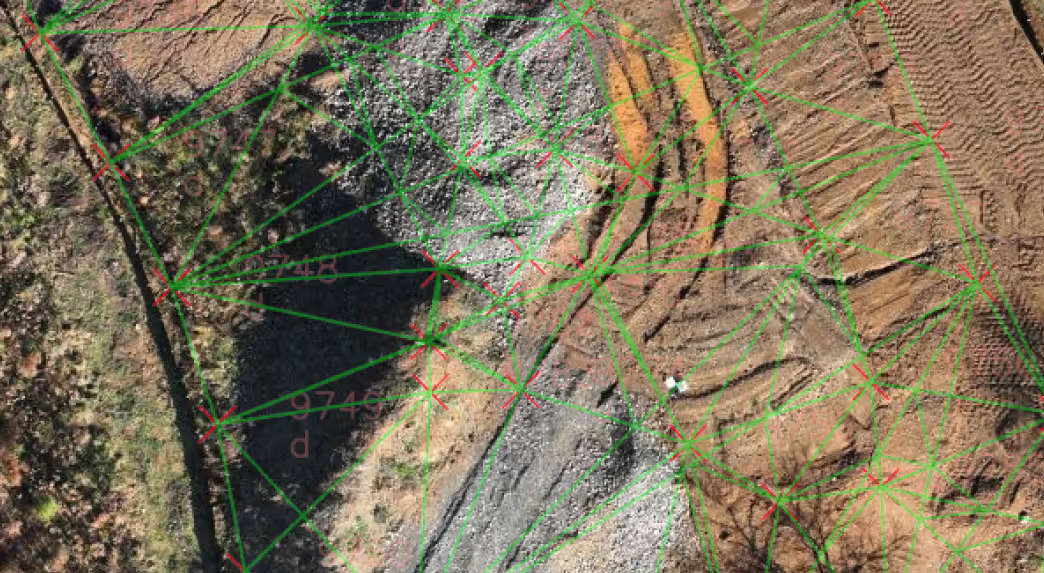
When the team turned Crosshatch 3D off, they were able to capture nadir images in a parallel hatch at a -90 degree gimbal angle. Lastly, the team activated DroneDeploy’s Enhanced 3D mode flight mode to allow for a combination of oblique and nadir by capturing imagery in a parallel hatch with the gimbal at -90 degrees.
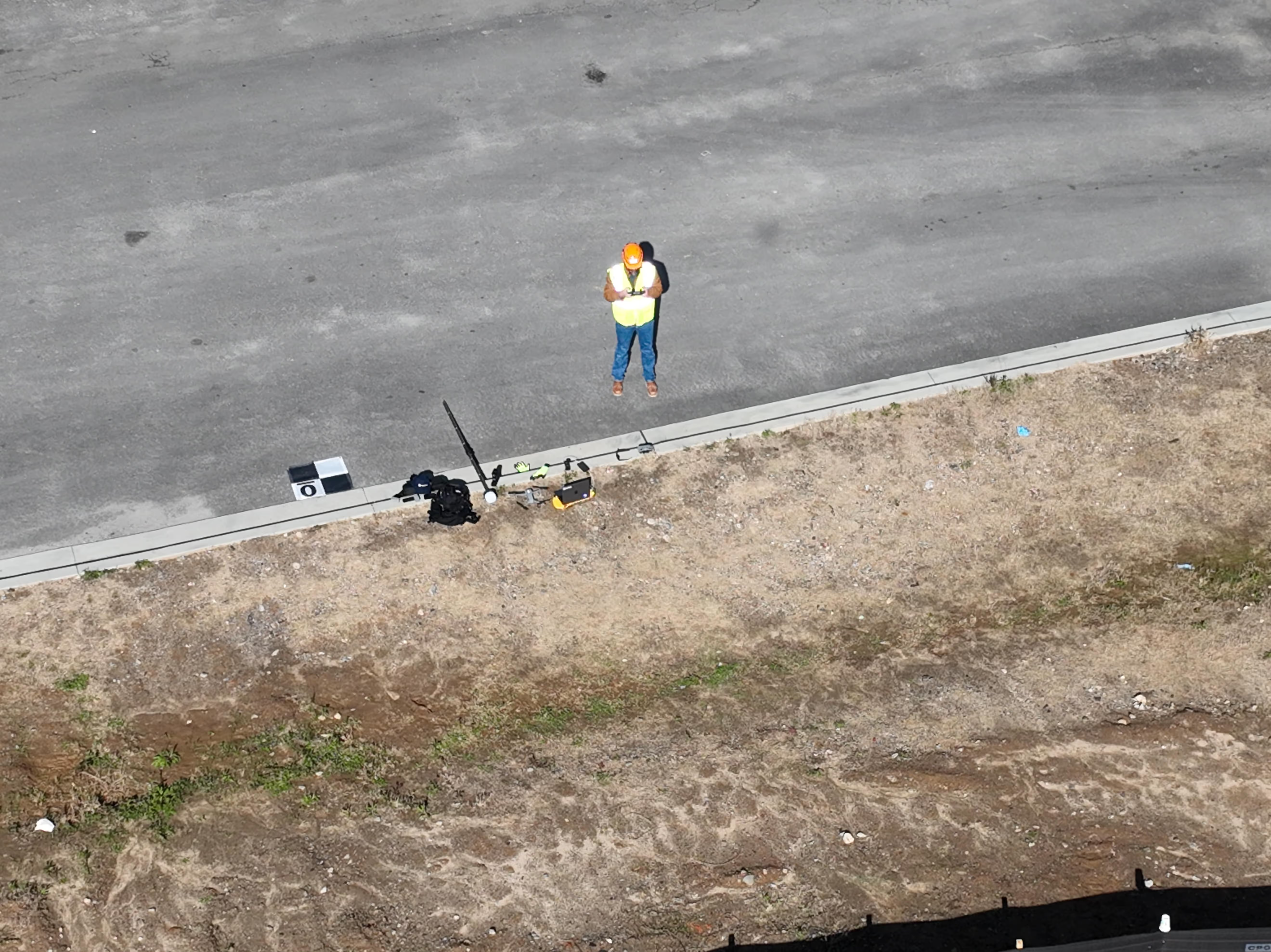
Captured imagery was then uploaded to Autodesk Civil 3D so the Archer Western team could triangulate their base plane to the other ground control points. Captured images were also processed in DroneDeploy, where the team applied its volume annotation tool.
Georeferenced models and design surfaces were also brought in to ensure comparison base planes and stockpile takeoff extents were equally compared.
The ground control point (GCP) files were concurrently uploaded to ensure centimeter-level map alignment. Once prompted to tag and confirm ground control point locations, all GCPs were tagged in at least eight photos. And flights that included data with RTK corrections were reprocessed again and automatically processed with PPK.
.avif)
Averaging accuracy across workflows
The Archer Western team discovered that drones presented stark differences in terms of sheer visibility into the stockpile, as DroneDeploy was able to capture over three million points of data compared to the 65 points captured with traditional surveying equipment.
This supports the view that traditional surveys are unable to account for any curvature or unsurveyed anomalies to a stockpile, as they can only calculate straight lines via triangulation.
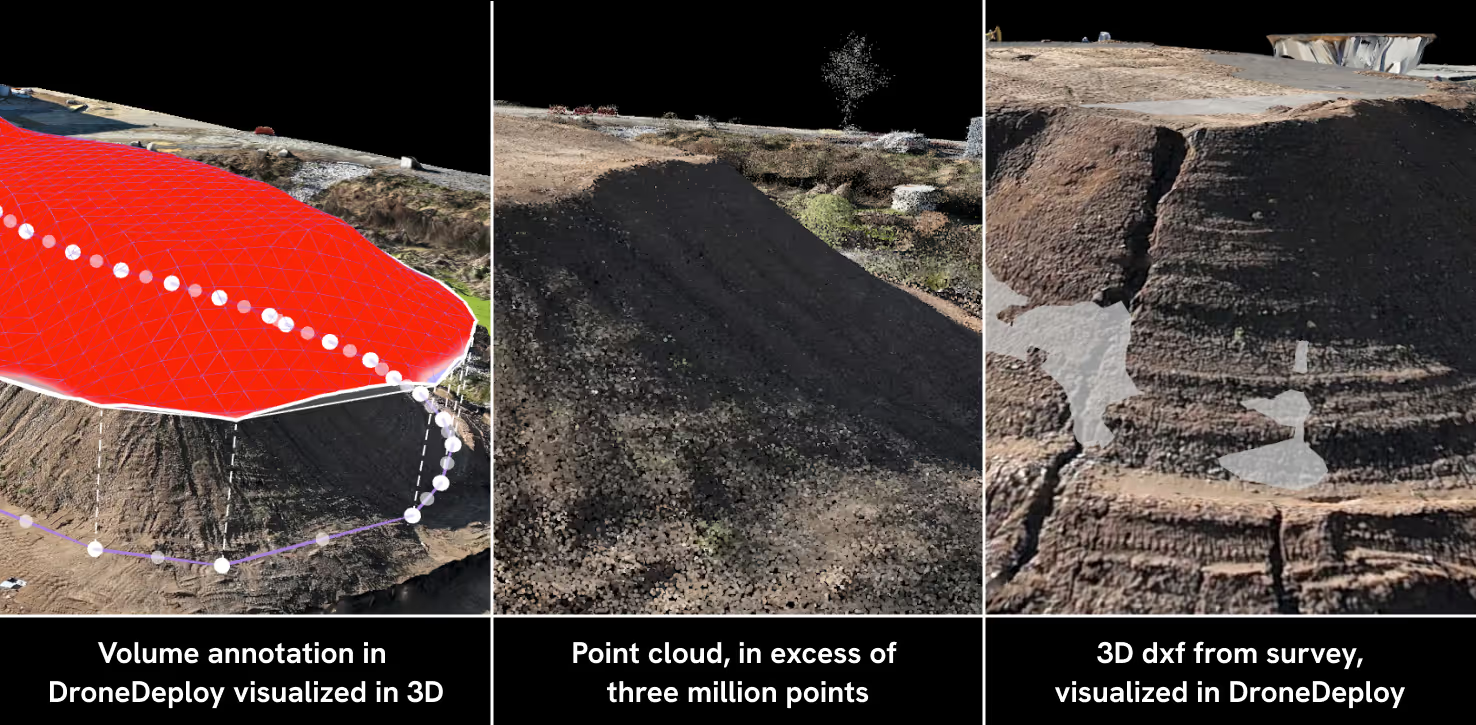
Georeferencing via GCPs
Establishing high-accuracy workflows and checkpoints is crucial to uphold map precision and ensure map accuracy. Even so, incorporating ground control points does not demonstrate statistical significance in validating stockpile volumes, particularly when users integrate georeferenced layers and overlays into DroneDeploy or assess precise changes to maps over time.
While GCPs appear to marginally enhance the relative accuracy of this stockpile, Pablo and his team did not uncover a statistically significant difference in Relative Accuracy between using GCPs or not for stockpile measurements.
.avif)
Oblique and nadir imagery serve different purposes
While the different types of imagery captured didn’t show statistically significant deviations when flown at 200 feet above ground level (only a .18% delta between GCP and non-GCP flights), there were benefits to triplicating image capture: with nadir images alone, the Archer Western team could view all surfaces of their stockpile whereas oblique images enhanced visibility on surfaces obstructed by heavy shadows or vegetation.
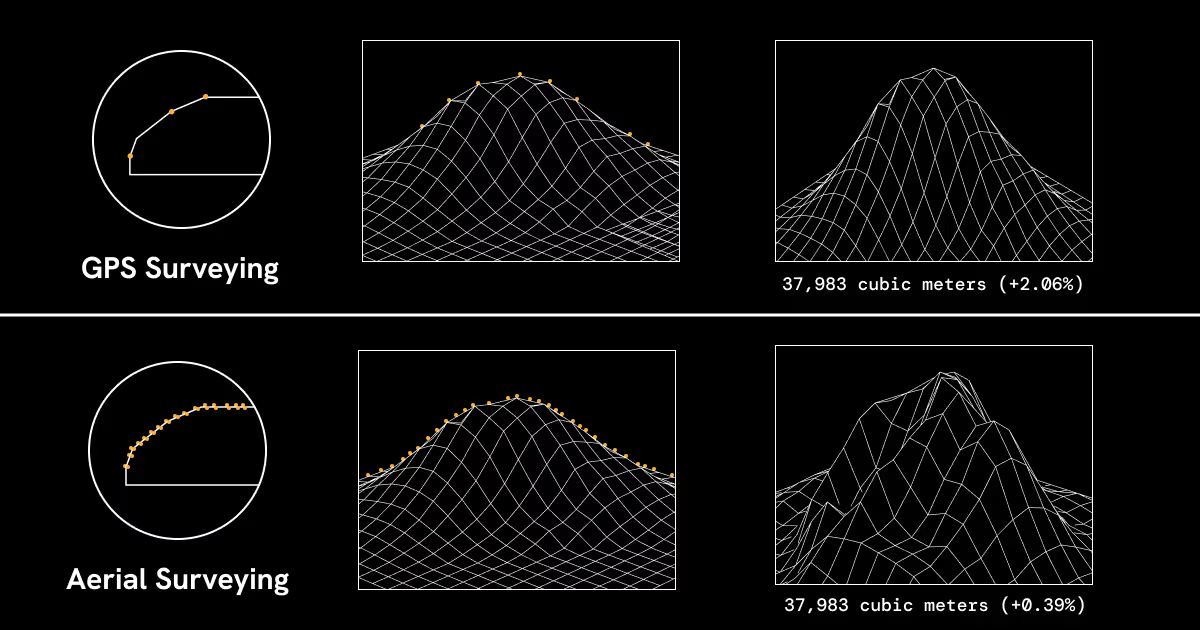
While traditional surveying equipment remains essential, Pablo and Archer Western have grown to rely on DroneDeploy to obtain precise measurements into their materials stored on site. They’ve seen how integrating drone technology streamlines traditional workflows in ways which serve multiple purposes.
For one, drones enable Archer Western to avoid putting people on a pile to obtain its full dimensions. Whether using the Air 2S or Mavic 3 Enterprise, DroneDeploy helps their team achieve reliable relative accuracy, whether or not they implement high-accuracy (but time-intensive) workflows such as GCPs, RTK, or PPK.
Ready to take your drone maps to the next level? Download the Complete Guide to High Accuracy Drone Mapping.