16
cities with regional offices
20+
staff drone pilots nation-wide
152
years in business
Large construction companies like McCarthy are increasingly using drone maps and models to streamline and enhance workflows on complex projects, often saving thousands of dollars in man hours along the way.
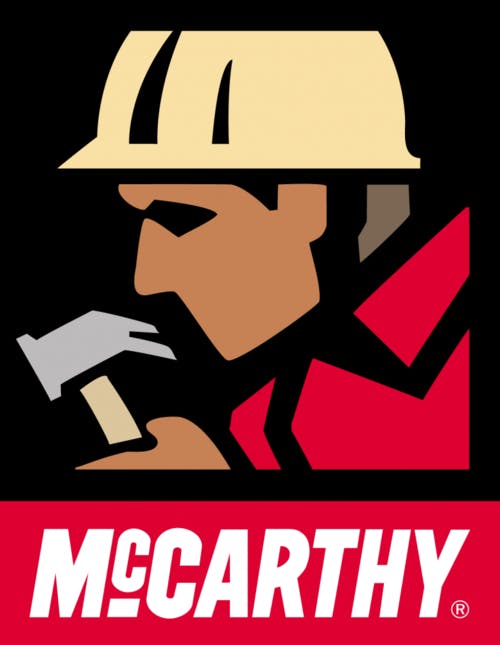
Scaling an enterprise drone program to 20+ pilots requires an enterprise approach: Standardizing training, building protocols and ensuring safety. McCarthy Building Companies rose to meet these challenges, implementing an enterprise drone program that grew from a single drone to a fleet of 20 in just shy of a year. They plan to expand even further.
This success is thanks in large part to their innovative Drone Champion Program , a company-wide task force that carefully thought through every aspect of integrating drones into the company’s job sites. This construction giant continues to find new and innovative ways to use drones to improve efficiency, communications, and data analysis on complex building projects.
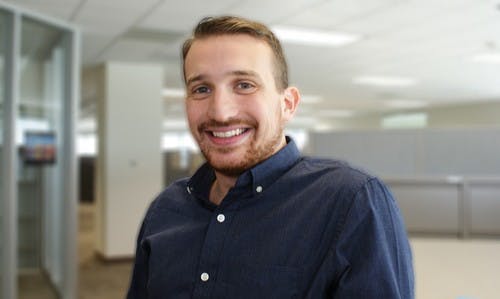
Ryan Moret (Field Solutions Manager) discusses how McCarthy Building Companies developed a thriving enterprise drone program and the carefully planned approach that led to its success.
McCarthy specializes in large, complex construction projects for the healthcare and education sectors, renewable energy, and more. They are one of the largest domestic builders in the US, with regional offices in sixteen cities. The company’s field solutions, BIM, survey, risk management, and solar teams all leverage drone maps and models in their work.
If you attended our Drones in Construction webinar series, you heard Ryan talk about the process he and other McCarthy staff underwent to launch the company’s enterprise drone program.
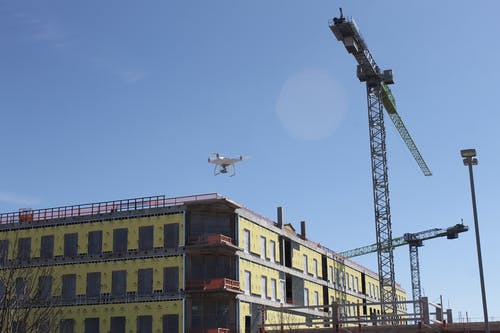
Laying the Foundation for a Successful Enterprise-Level Drone Program
Flying a single drone is one thing, but scaling that operation across the entire country is quite another. “We didn’t want individual job sites to go out to the local hobby shop,” Ryan says, “pick up a Phantom 4, and go fly it out there without the proper licensing, insurance and training.”
Putting any new technology into place can be a lot of work, especially when it’s something like drones that often have safety concerns, privacy concerns…It was something we had to come at very tactfully.

Ryan Moret, Field Solutions Manager, McCarthy Building Companies
They created the Drone Champion Program to leverage expertise from all levels of the company. This task force intentionally involved at least one person from each of the company’s five divisions, as well as representatives from risk management, legal and operations. The task force spent four months laying the groundwork before the first drone ever took flight at a McCarthy job site.
The group stayed open to the possibility of contracting out drone services on a case-by-case basis. To plan for this possibility, they created a contract template and a list of insurance requirements for drone service contractors. This thorough, plan-ahead approach allows McCarthy’s drone program to remain agile, able to meet the varied needs of each individual project. Today, the company occasionally hires third-party drone services when it isn’t feasible for onsite staff to gather drone data themselves.
The ease of using drone software programs like DroneDeploy allows staff to gather drone data during the course of a normal workday and incorporate that data into existing workflows, using industry software like Autodesk, and Box and Skyward. DroneDeploy’s App Market allows them to do this with ease, connecting drone maps to top industry solutions directly within the DroneDeploy dashboard.
The Drone Champion task force developed a comprehensive set of operations policies and safety protocols, as well as an ongoing staff training program. A year into their program, the task force continues to play a vital role in the company’s UAV program. When a new project comes online, a representative helps staff through the process of choosing a drone, evaluating any site-specific safety concerns and providing ongoing training around hardware and software. All of this behind-the-scenes work helps projects maximize the effectiveness of their drone data, all the while maintaining job site safety and the integrity of critical operations.
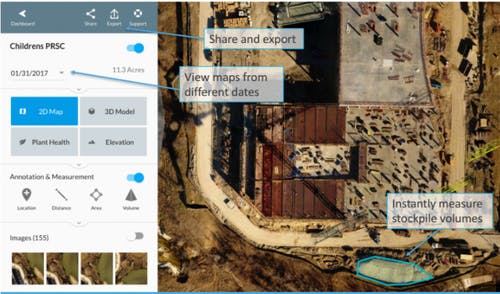
Drone maps and models, combined with DroneDeploy’s tools for analyzing and sharing data, improved efficiency, communications and data management on a $65M hospital project in north Dallas.
Tackling Complex Projects With the Help of Drone Data
McCarthy staff uses drone data to improve the day-to-day workflows on their job sites. “We handle very complex projects,” says Ryan. “They are large and they have a lot of moving parts.” From start to finish, drone data streamlines these complex processes. They've made it possible in several ways...
Standardized data capture
As routine practice, McCarthy projects map their job sites each week through a series of three drone flights: a standard mapping flight; a manual flight to capture the additional orbitals needed for 3D models; and a fly through video, which is a favorite of the company’s marketing team. The entire process takes less than twenty minutes.
DroneDeploy’s automated, repeatable flight plans allow site staff to create a consistent set of data week over week. This automation is also useful from a risk management standpoint.
We like using the automated systems because it opens up less opportunity for risk. With confidence, I can walk out every week and do all three flights on the same SD card… send it to DroneDeploy for processing and have data back in a few hours.

Ryan Moret, McCarthy Building Companies
Complex analysis
To help analyze their drone data on the fly, McCarthy staff uses DroneDeploy’s native analysis tools, like volume and area measurements. “For what we’re doing on a commercial site, the measurement tools are killer,” says Ryan. “I can tell how many square feet of roof we’ve put down, how much square footage of concrete is left to pour. We can measure the volume of a topsoil stockpile. If we’re trying to figure out truck access, we can measure the width of a road or gate or how much room we need to clear out for material to make the site clean and organized.”
For more complex analysis, staff integrates drone data into their existing workflows. “We can export any data we see in DroneDeploy into industry software,” Ryan points out. This includes exporting data into the Autodesk suite to manipulate and change images, conducting visualizations using obj. files for more robust workflows, and easily integrating everything into Box for improved project management.
Information sharing
Ryan says one of the greatest benefits of drone software is the way it helps McCarthy’s large teams share information with ease. Drone maps and models, along with annotations and analysis, are easily shared with internal and external stakeholders.
“At the end of the day, we’re coordinators and communicators,” says Ryan. “We pull a lot of people together to try to build very complex jobs, and we can’t do it alone. We want the best product for our clients at the end of the day, so communication and collaboration are very important to us.”
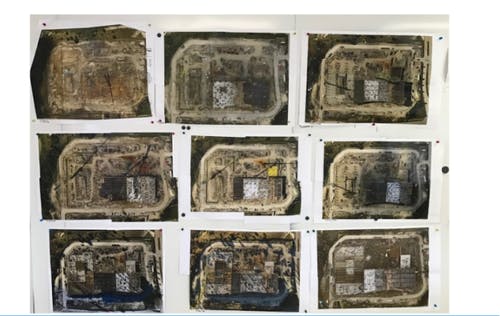
McCarthy’s Map Wall Improves Communication and Coordination with Drone Imagery
If you really want to get a sense of the difference drones make on a construction job site, look no further than McCarthy’s “famous map wall." Despite the many high-tech ways McCarthy teams use drone data, “paper is still the common denominator for job sites,” Ryan says. On every McCarthy site, the wall of the job trailer is covered with weekly drone maps posted in sequence, giving anyone who walks into the room a clear picture of the project’s progress over time, as well as a snapshot of any current issues on the site.
The trades love it, being able to walk up to the wall and see nine weeks of construction photos. They pull these up in every sub meeting, and every owner meeting. We have data from that week to show contractors, ‘Hey, the site’s a mess, you guys need to go clean it up.’ You can see rebar spread out all over the place, so there’s no arguing. They see it for what it’s worth.

Ryan Moret, McCarthy Building Companies
When a higher-tech solution is in order, Ryan’s colleagues overlay design documents with a drone map using industry software like Bluebeam, creating a simple and effective way to explain production issues to owners.
“Not all of our owners speak construction,” Ryan points out. “So they walk out and they just see a mess of concrete and material and they’re not sure what we’re doing. So it helps to take the paper documents they’re used to seeing, the design documents they’re used to seeing, and show them what we’re working on and why we need what we need.”
“Drone maps and models,” says Ryan, “bring the planned world into the real world and make it easier for people to digest.”
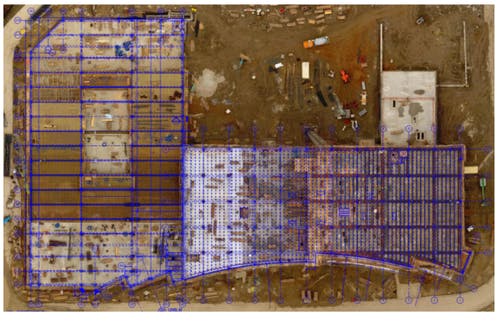
The Future of McCarthy’s Enterprise Drone Program
In short: they crawled, they walked and now it’s time to run. Given the success of their drone program so far, the company intends to expand their fleet and how they use drone data.
McCarthy’s Dallas team has begun using DroneDeploy for stockpile analysis. The St. Louis team is using drones for earthwork tracking. They're leveraging drone data on solar sites by using infrared imaging for testing building enclosures. The teams are pleased with the accuracy of the results and strong return on investment.