Pre-Construction
Benefits of reality capture in pre-construction
Communicate existing conditions to bidding trade partners
All images are mapped by date and location for future reference
Give stakeholders higher confidence in their proposal
Help the trades to coordinate prior to mobilization
Communicate important site logistics (e.g. laydown areas, parking, storage, offices, connex, dumpster locations)
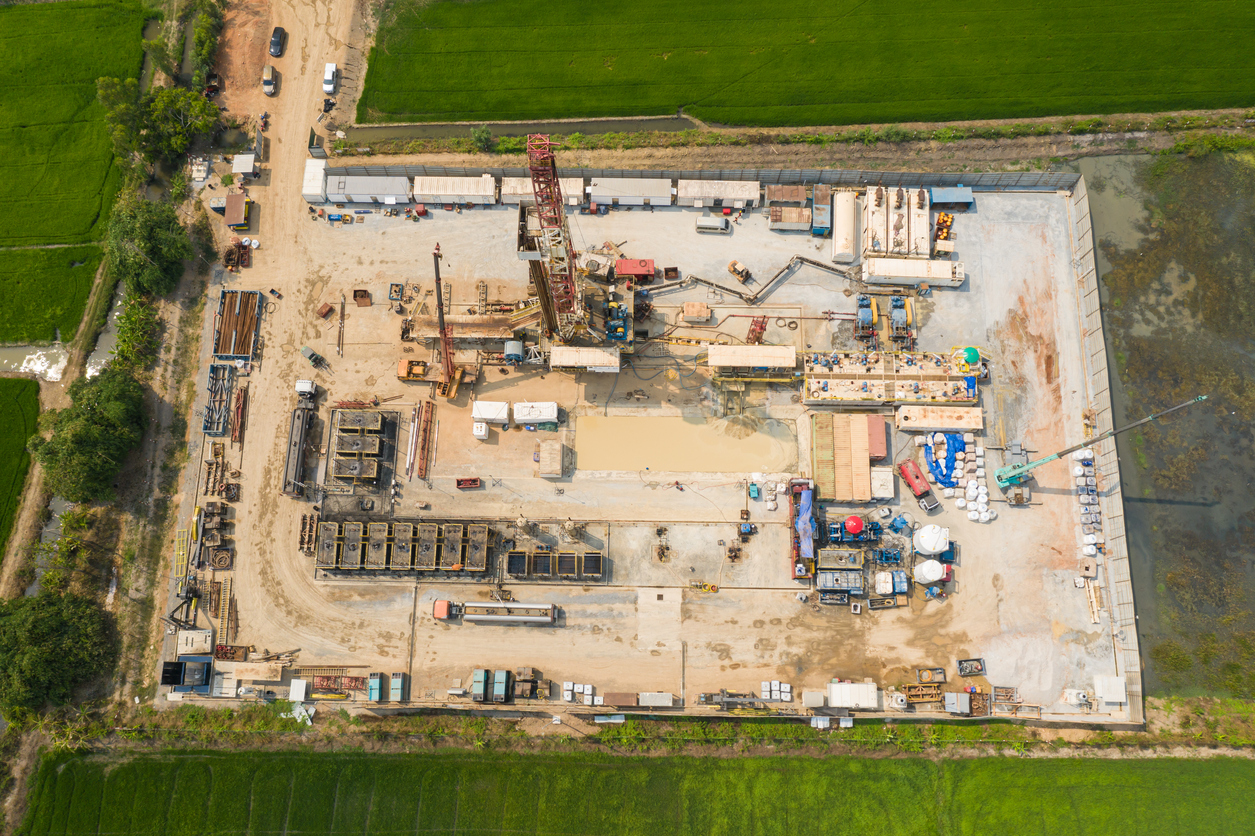
Pre-site survey
Use reality capture to document existing site conditions prior to mobilization. Survey data can be shared with the project team, trade partners and other consultants to ensure everyone is familiar with the site.
Additionally, include a PDF of survey data in the contract for a comprehensive overview of the site.
Above ceiling investigation
Use reality capture to ensure that exploratory conditions, tie-in locations and equipment locations are all documented in an organized manner. This will provide a comprehensive site overview and aid in planning.
Enhanced site logistics
Capture access points, parking, loading zones and laydown areas for coordination prior to mobilizing. This information can be shared with the team and partners to ensure a smooth and efficient construction process.
Construction
The value of frequent reality capture throughout construction
Virtual access to the jobsite for internal team and stakeholders (architects, owners, etc)
Reference images for use during OAC meetings, trade partner meetings and daily huddles
Resolve trade damage claims
Mitigate risk and minimize rework
Stay on budget and on schedule
Substructure
Earthworks
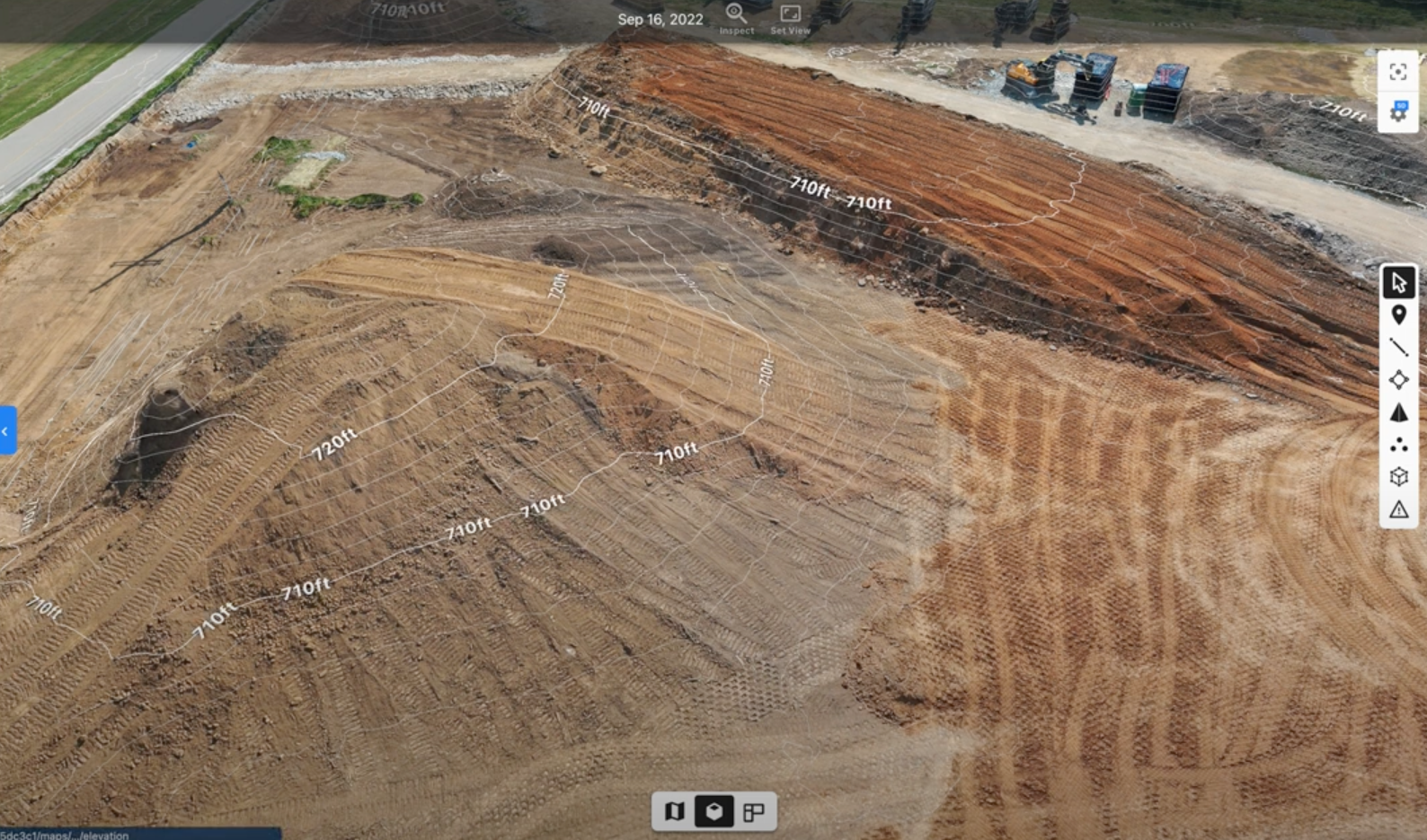
Critical capture milestones
Quantity reports
Cut/fill analysis
Overall site progress
Why it's important
Reality capture provides accurate snapshots of how much earthwork is on site at any given date. Compare progress over time. Contractors gain insights about the area’s topography and receive a survey that’s accurate down to the centimeter. Use DroneDeploy to produce an exact high-resolution map and 3D model of a job site – all processed in a matter of hours.
Underground utilities
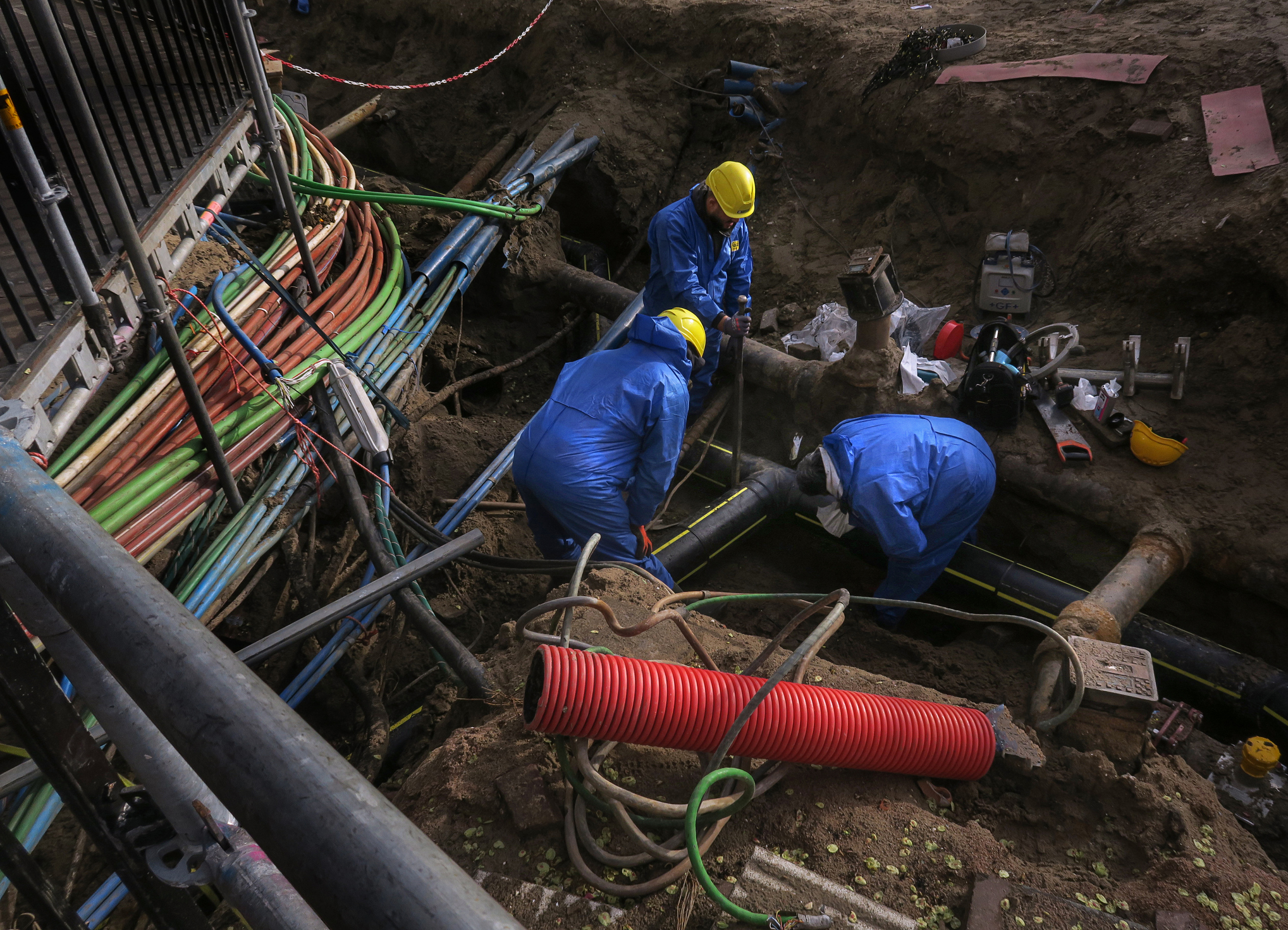
Critical capture milestones
Existing conditions
Utility installation
Backfilling
Final grade
Why it's important
Reality capture of underground utilities means you'll be able to view components that have been covered later. This makes it easier to coordinate logistics with trade partners, including turnover of the site to the concrete vendor.
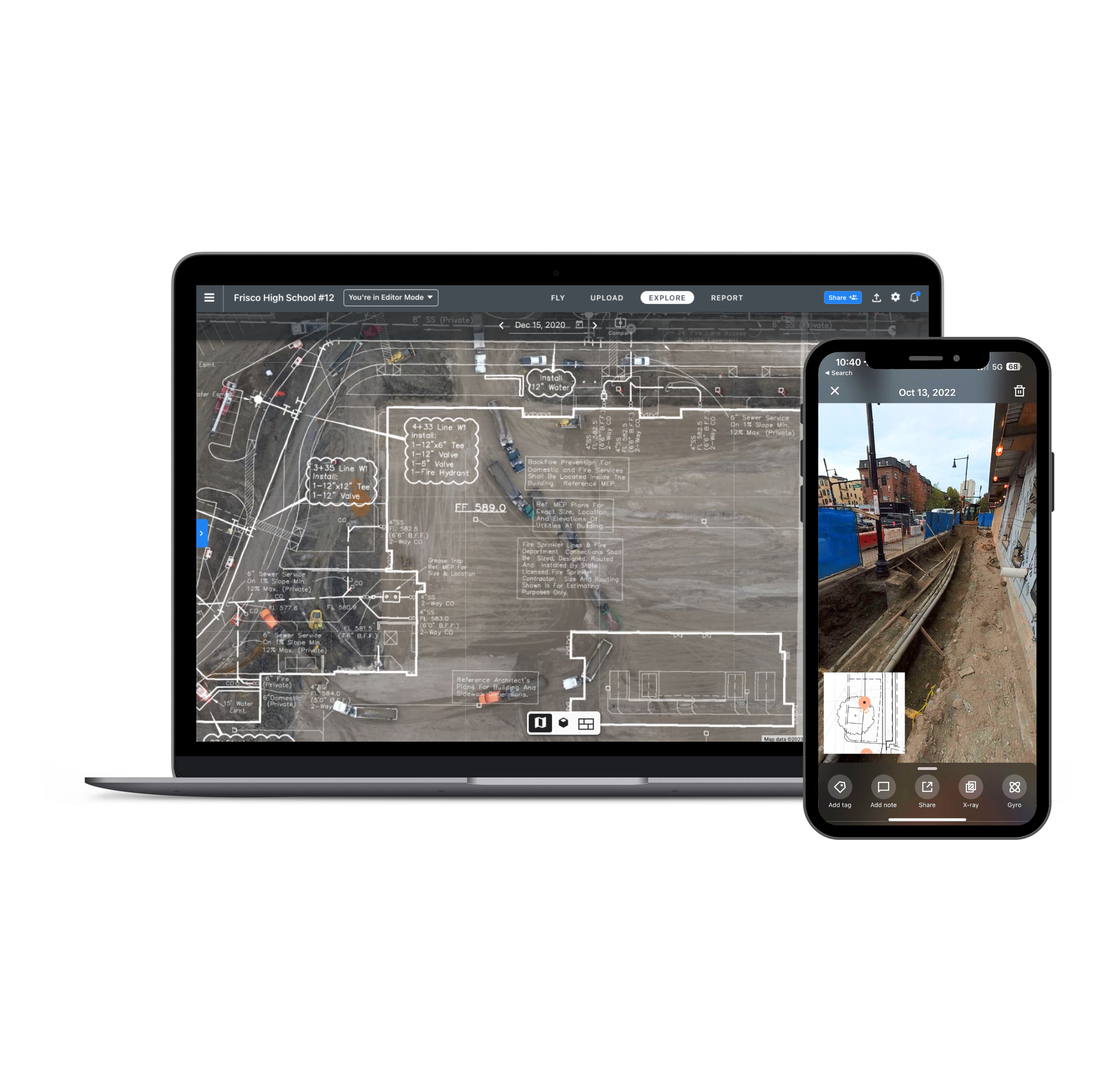
Measuring material for removal
Reality capture at this phase can be useful for determining the root cause of efflorescence, spalling or water intrusion.
For example, water intrusion in the site work section such as tears, holes, and improper installation of vapor barriers can be documented with DroneDeploy.
Foundation
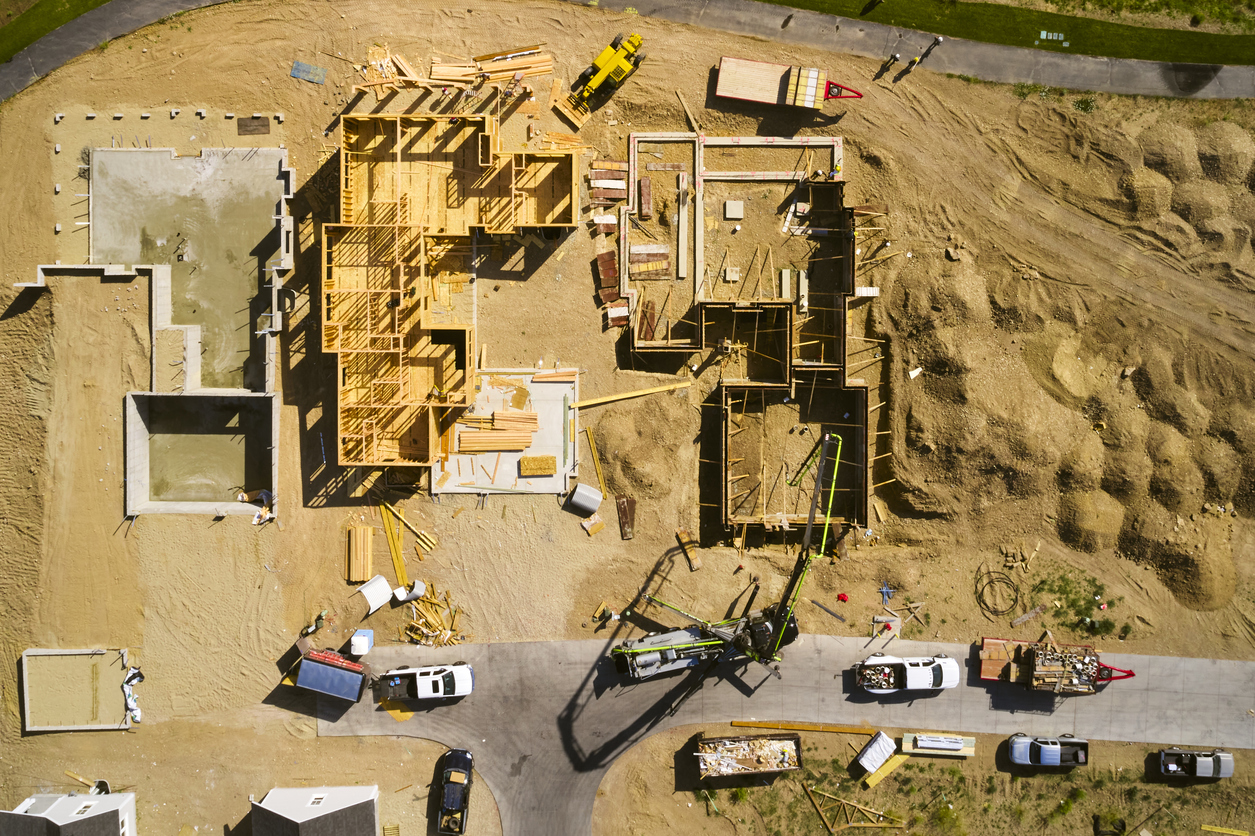
Critical capture milestones
Drilled piers
Foundation walls
Grade beams
Why it's important
Capturing the location of structural elements means you can ensure everything is in the right location before concrete is permanently placed.
View aerial imagery to get a holistic view of progress as foundations are being installed. Or use ground 360 imagery to inspect work installed and validate installation of key structural elements.
Structure
Concrete structure
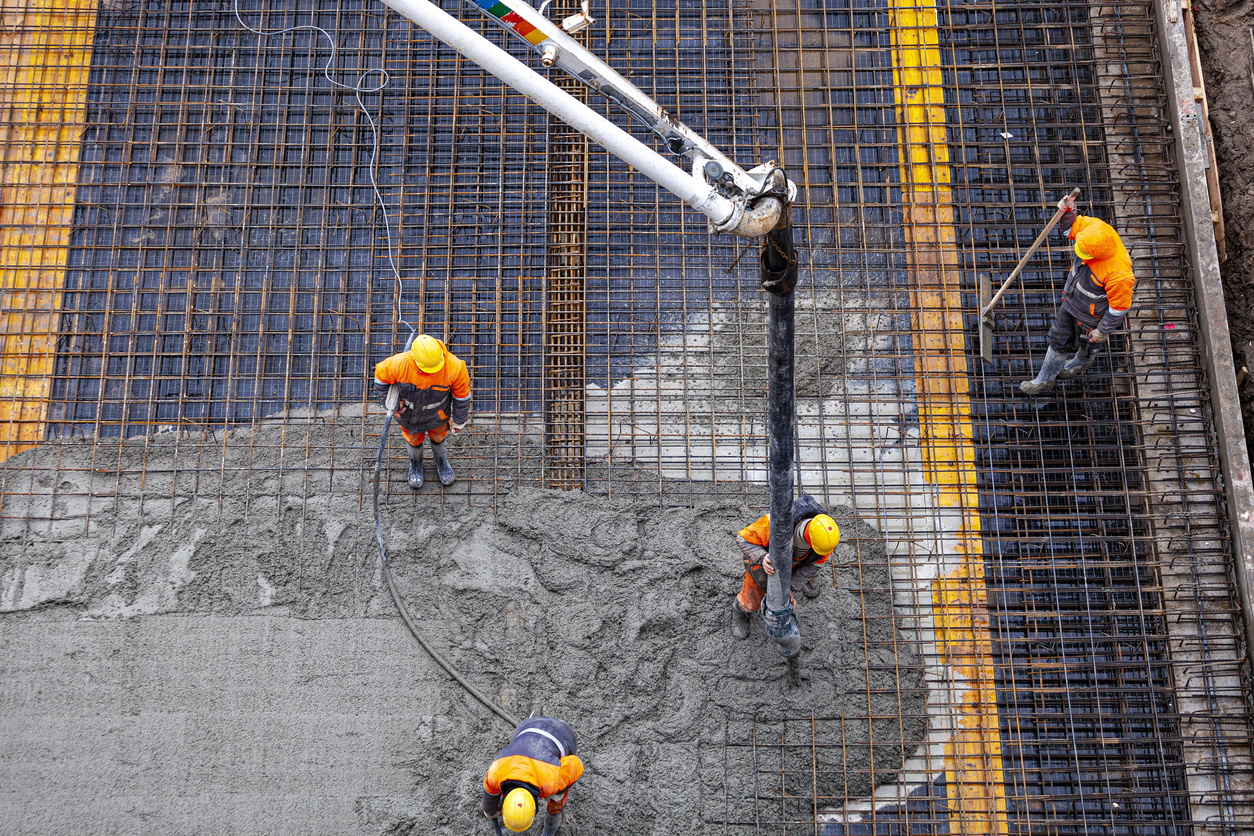
Critical capture milestones
Rebar/post tension cables
Blockouts
Slab edges
Slab depressions
Mechanical sleeves
Steel embeds
Why it's important
After concrete has been placed, you can find missing sleeves or spacers, check forms for cleanliness and know where rebar and post-tension cables are in the slab – especially in the event core drilling is necessary.
This also allows VDC engineers to QC penetrations remotely, and it reduces the need for costly slab scanning.
Traditional surveys take weeks to complete and
only provide linear point data. With DroneDeploy's photogrammetry mapping, we get elevation data
to create plans for equipment placements and
pump sizes for fluid pump selection.
This data is very accurate and creates quick turnaround
times for design proposals, allowing us to
make faster decisions.
Steel Structure
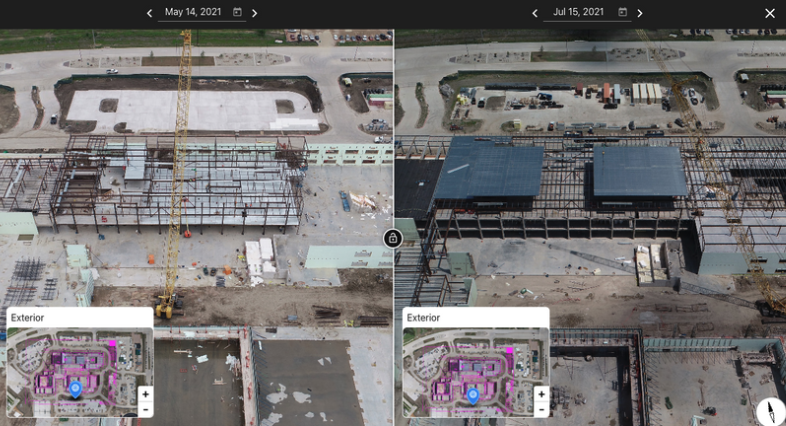
Critical capture milestones
Steel beam and column installation progress
Detailed miscellaneous steel connections
Metal decking
Structural deck pours
Why it's important
Visually documenting progress of structural steel and decking on a weekly or monthly basis can help with quantity and schedule comparison.
Reality capture also aids with the verification of work completed, since the majority of the connections/members will be covered up by other elements in future phases.
Exterior
Facade
Critical capture milestones
Progress of exterior framing
Waterproofing details
Wall System installation
Exterior penetrations
Exterior punchlist
Why it's important
Reality capture allows you to efficiently check the installation and quality of work at key exterior milestones.
With DroneDeploy, you can send drones on autonomous inspection missions to capture building exteriors – keeping team members out of dangerous conditions.
Automated Facade Flights
Manually flying a façade can be challenging and cumbersome.
DroneDeploy makes this process easy, efficient, automated – and most importantly, safe.
Roofing
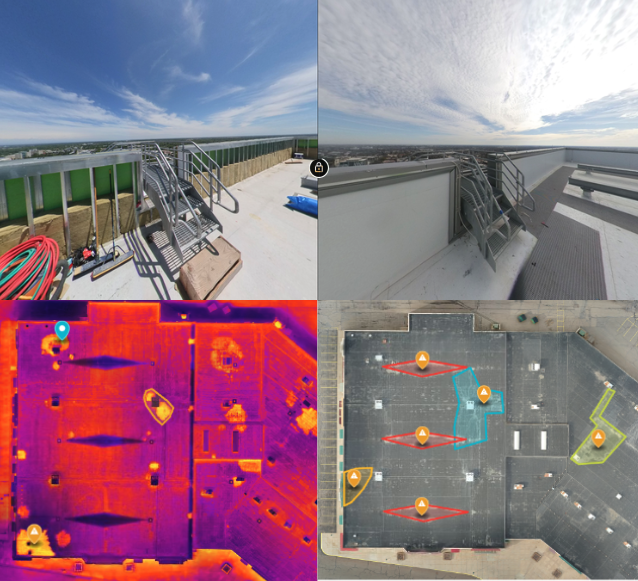
Critical capture milestones
Quantity measurements of roofing progress
Final condition of roof at hand off
Insulation lay down areas and installation
Roofing membrane installation
Penetrations and roof drain install
Complex waterproofing transitions
Why it's important
Water intrusion is a common problem in construction. It can lead to serious issues such as mold growth, deterioration of building materials and structural damage.
Reality capture can help to resolve water issues, as the quality of work in place can be verified without having to open up the roofing system.
Interior
Interior framing

Critical capture milestones
Wood Backing locations
Wall penetrations
Misc Steel locations
Pre-rock
Why it's important
Reality capture at this stage means that once drywall has been hung, you can look back at past dates to see what's behind closed walls. This helps you to avoid unnecessary rework and protect your business from future damage related claims.
Mechanical, electrical, plumbing, flooring (MEPF)
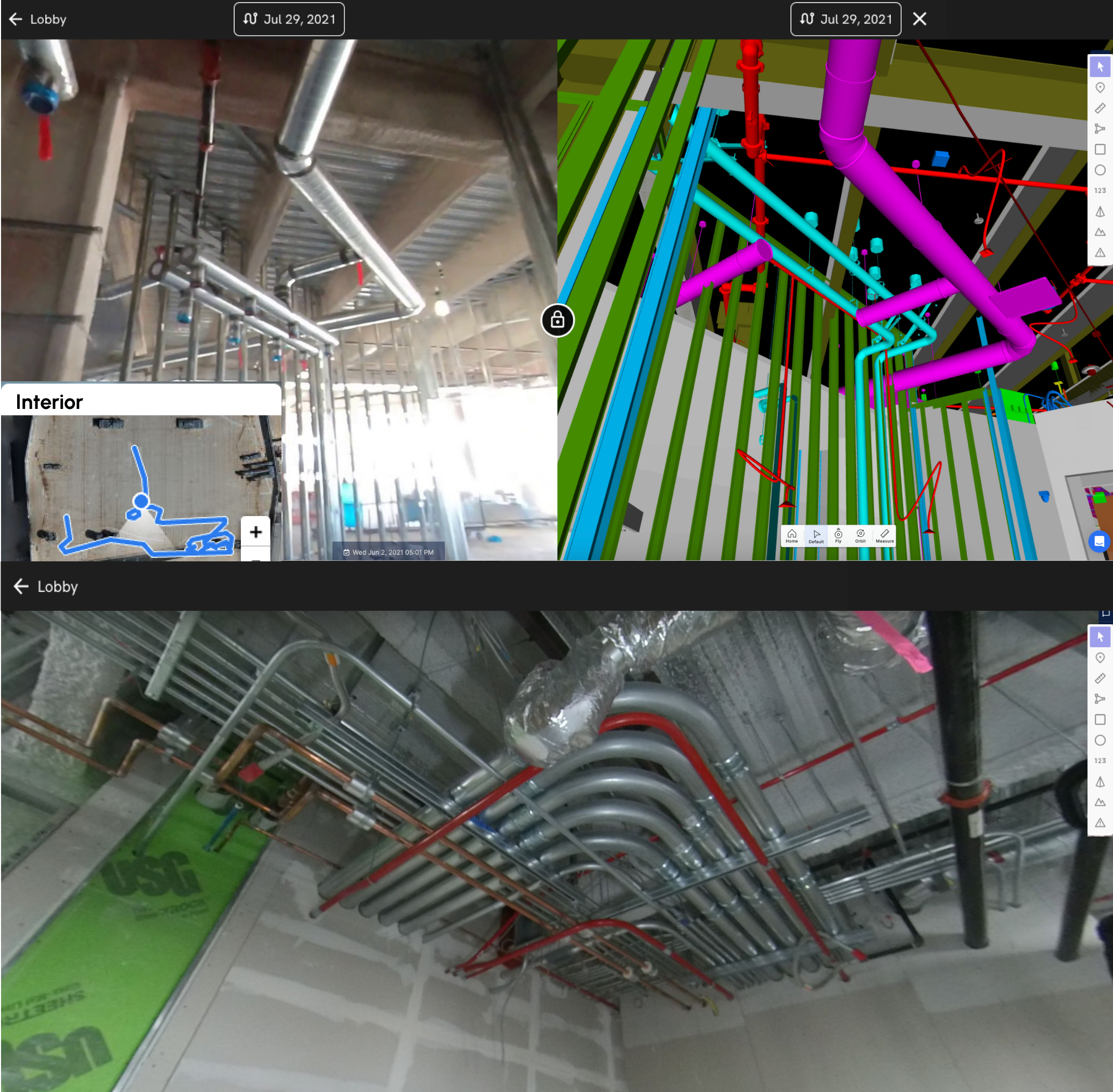
Critical capture milestones
In-wall mechanical, electrical, plumbing rough "in"
Fire/smoke/sound caulking and insulation
Pre-rock inspections
Mechanical penthouse & room progression
Why it's important
Reality capture at this stage means that once drywall has been hung, you can look back at past dates to see what's behind closed walls.
This helps you to avoid unnecessary rework and protect your business from future damage related claims.
DroneDeploy's timeline of images helped us identify wall penetration firestop issues. It also helped us verify if we inserted backing for our equipment. This saved us about $70-100k in time and resources.
Finishes
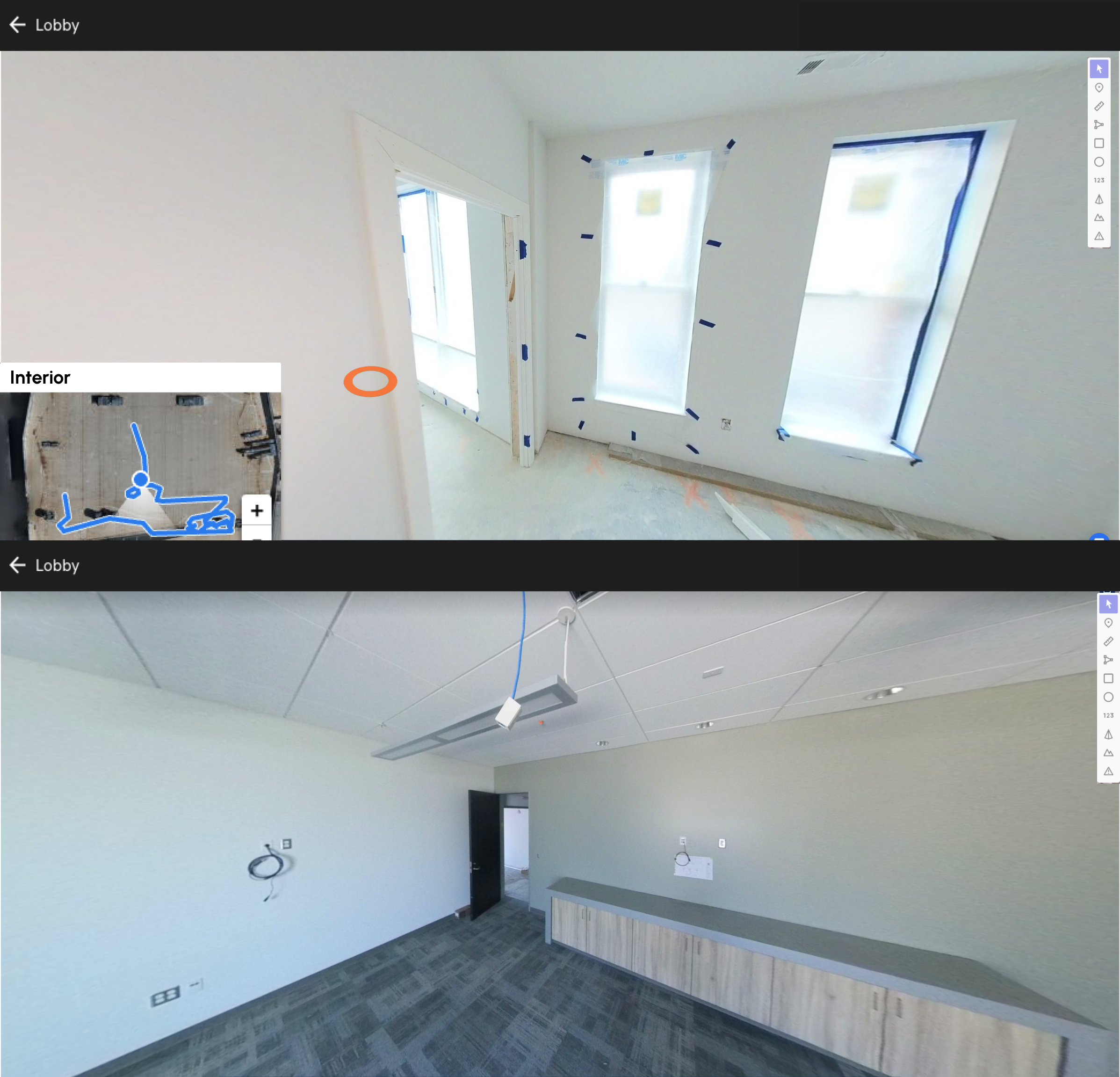
Critical capture milestones
Interior finishes
Paint, tiling, flooring, etc
Punchlist items
Floor turnover to owner
Turnover to external vendors
Why it's important
Reality capture at this stage records the condition and quality of final finishes; including paint, flooring, tiling and other decorative elements.
Prior to other people moving into the space, documenting conditions helps to combat a potential punchlist of issues created by external vendors.
Close-out
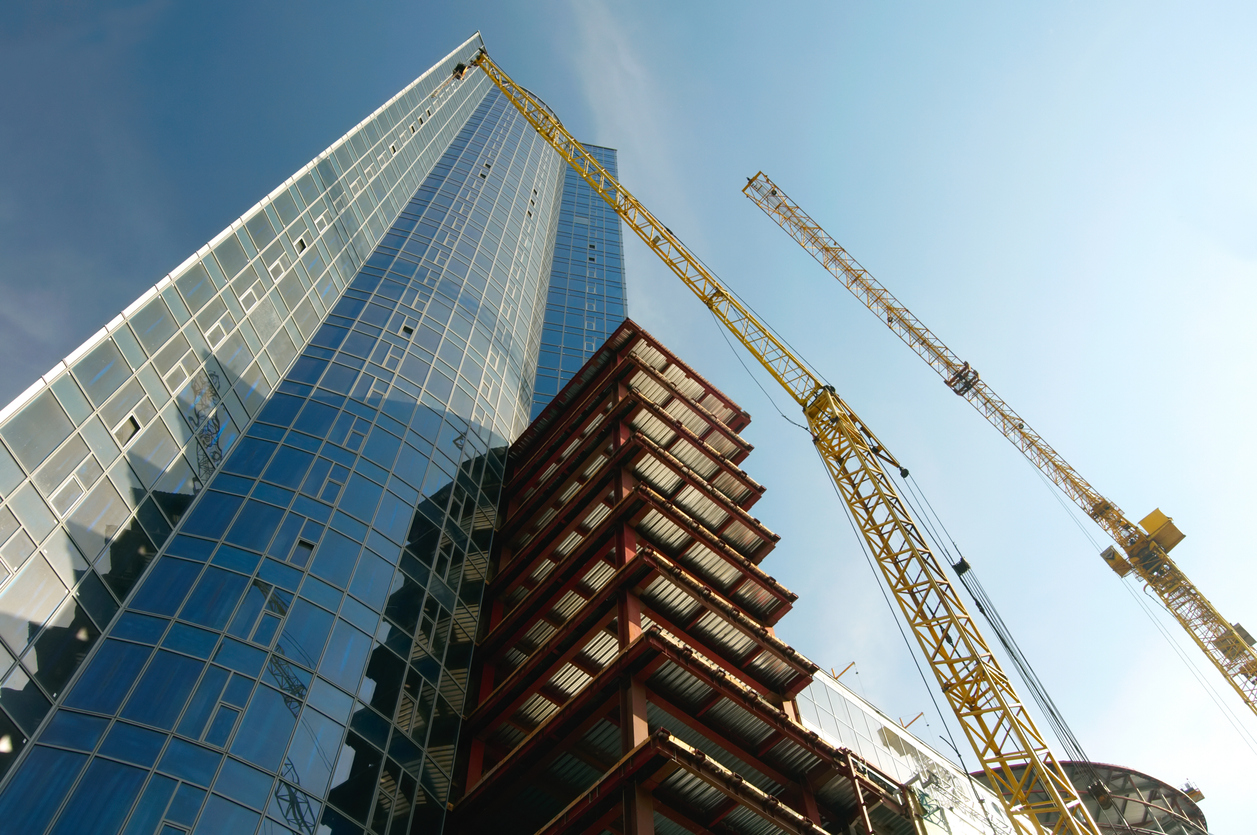
Close with confidence
DroneDeploy makes it easy to filter through photos you want to share, or export the entire document as an offline record for the owner at the end of the project.
Project Dashboard
With DroneDeploy, you have an internal company archive of all projects that can be used to reference with lessons learned and best practices when building similar projects.
A client was working remotely from Australia on a project that was based in Singapore. Visual verification of quality and completed work was easily carried out using DroneDeploy. Comparison between the design BIM and photos was also a good visual context for technical discussions.
The time savings estimated +500 man hours for a 6 month project.
David Pau, Project Manager | Obayashi Singapore
Unique Workflows Using DroneDeploy
Progress documentation
Best practices
Capture your job site weekly or bi-weekly. This will allow you to cover the most trafficked areas and reference back at any time stamp.DroneDeploy's SOP Guidelines can also help you establish your own best practices.
When to use the images:
Progress reports
Pay applications
Trade partner / OAC meetings
LEAN meetings
Marketing Pursuits
QA/QC
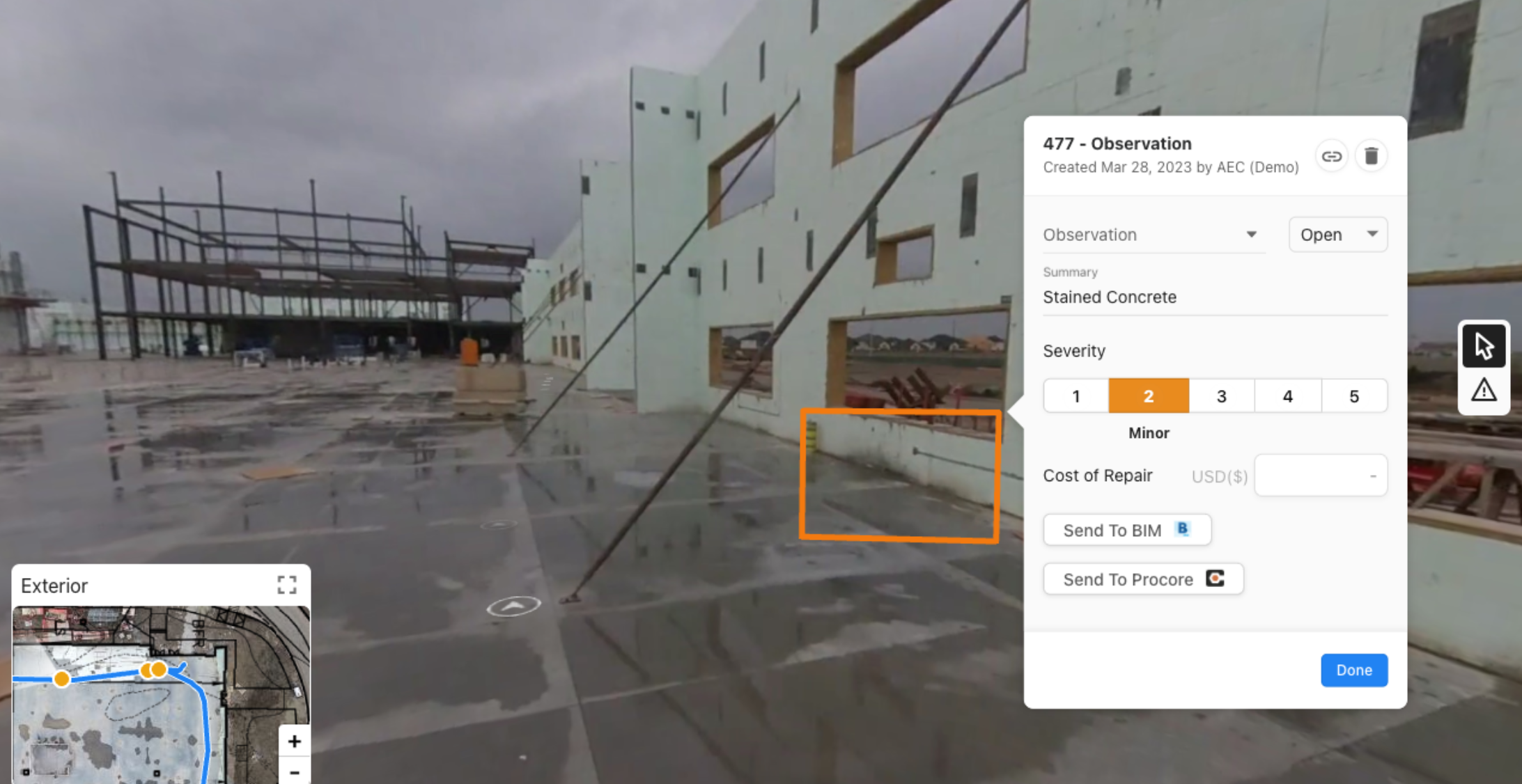
Best practices
Reality capture data can be used for monitoring work quality throughout the construction process, identifying and addressing issues and implementing quality control measures to prevent future problems.
When to use the images:
Inspection check lists
Preventing rework
Punchlist
Trade coordination
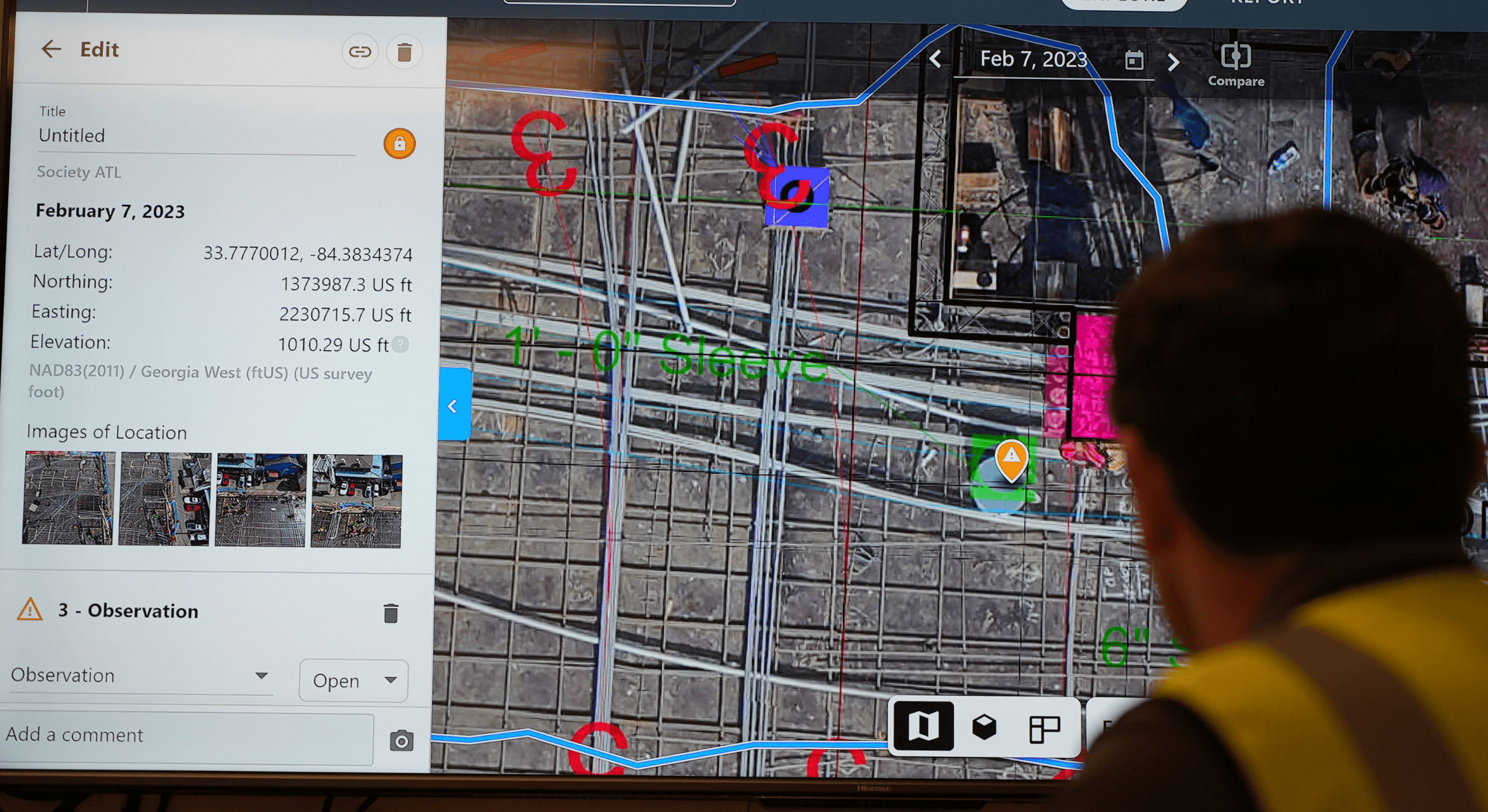
Best practices
Throughout the day, the hundreds of activities that take place are difficult to manage without having photos to use as a reference.
Use reality capture photos to talk through areas of the building as a helpful way of keeping everyone on the same page.
When to use the images:
Preconstruction bid reviews
Daily standup / huddles
Reviewing change orders / RFI's
Site logistics and lay down area
For our coordination meeting, we used photos almost the whole time. Now that the trades can see field conditions, it opens up entirely new coordination dialogue.
Progress documentation
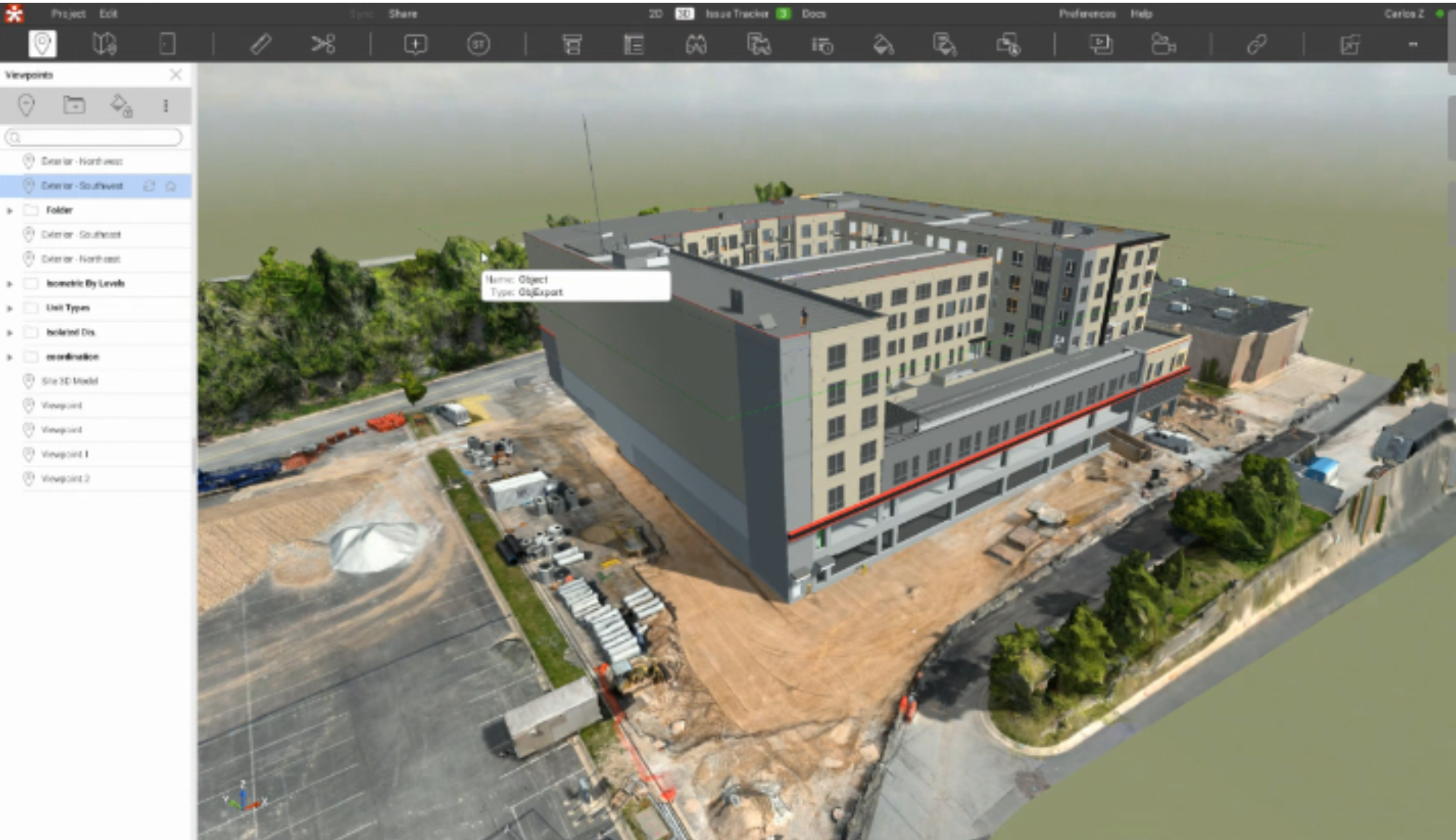
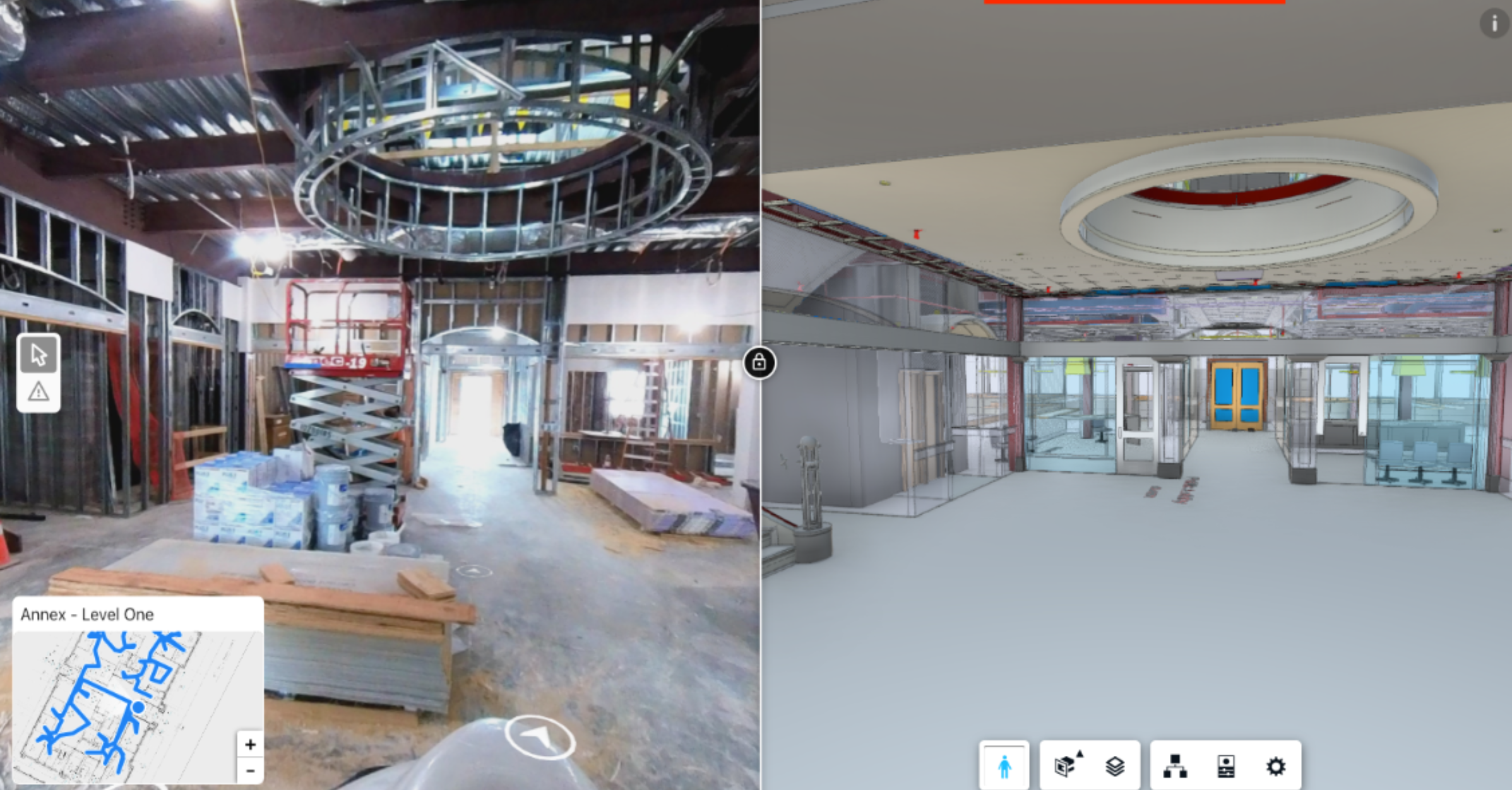
Critical capture milestones
Major equipment installation
Material storage (e.g. ensure duct is protected for certifications)
Why it's important:
Address quality control by integrating BIM coordination model
Logistics planning in tight areas
Use for coordination in weekly meetings
Export drone data into other platforms
Integrations
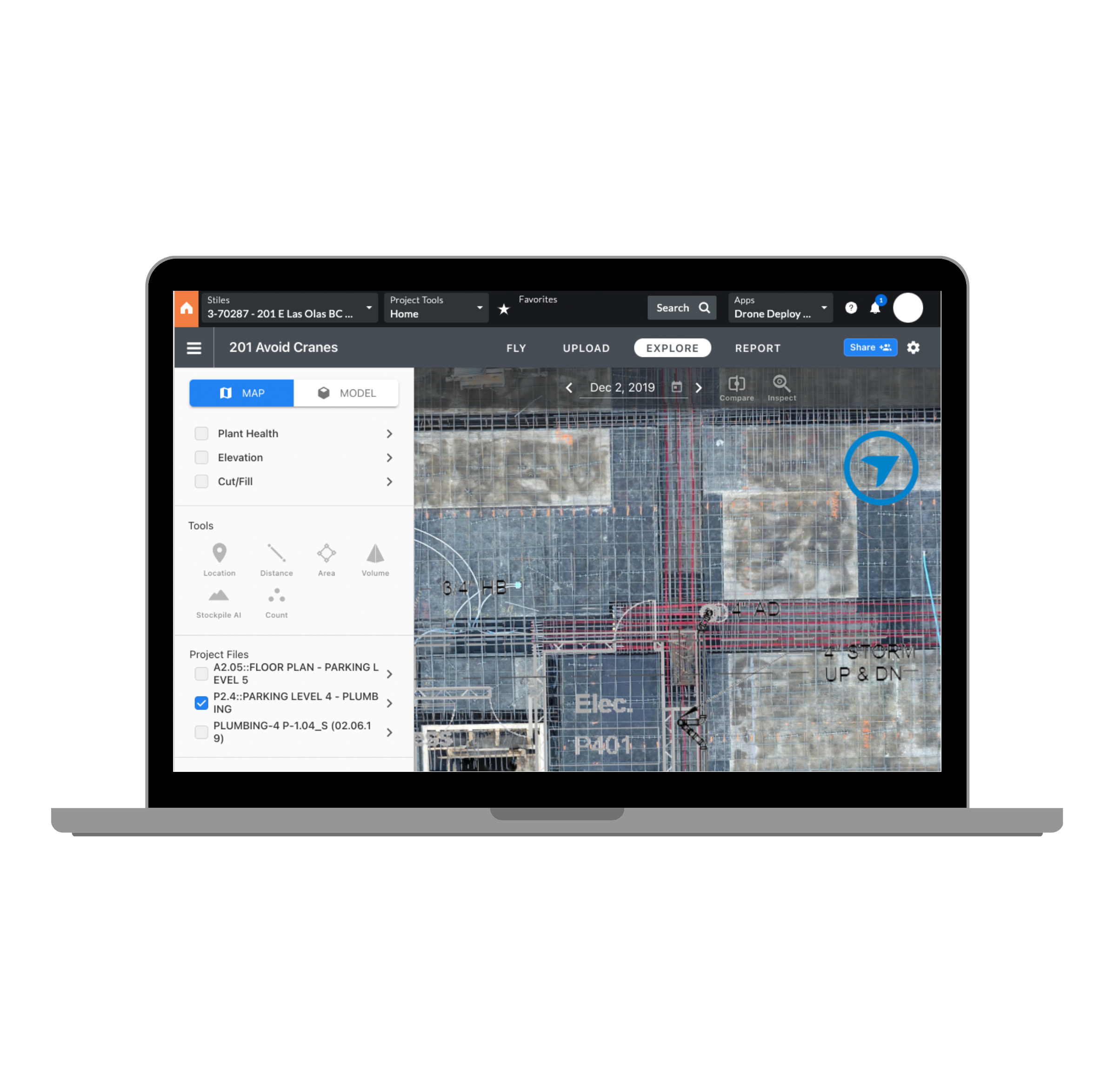
Procore
Create/add existing RFIs or observations
Embedded app experience
Single Sign On with existing accounts
Procore BIM comparison
Ability to sync drawings
Autodesk
Create/add existing RFIs
BIM comparison
Ability to sync issues
Embedded app experience
Ability to sync drawings
Single Sign On with existing accounts
Today, we’ve got everything linked with Procore - from a project’s floor plans, to its foundation, to its civil site utility drawings. And every time we have a revision, it's auto-synced from Procore into DroneDeploy.
Michael Gekas, VDC Director | McCownGordon Construction
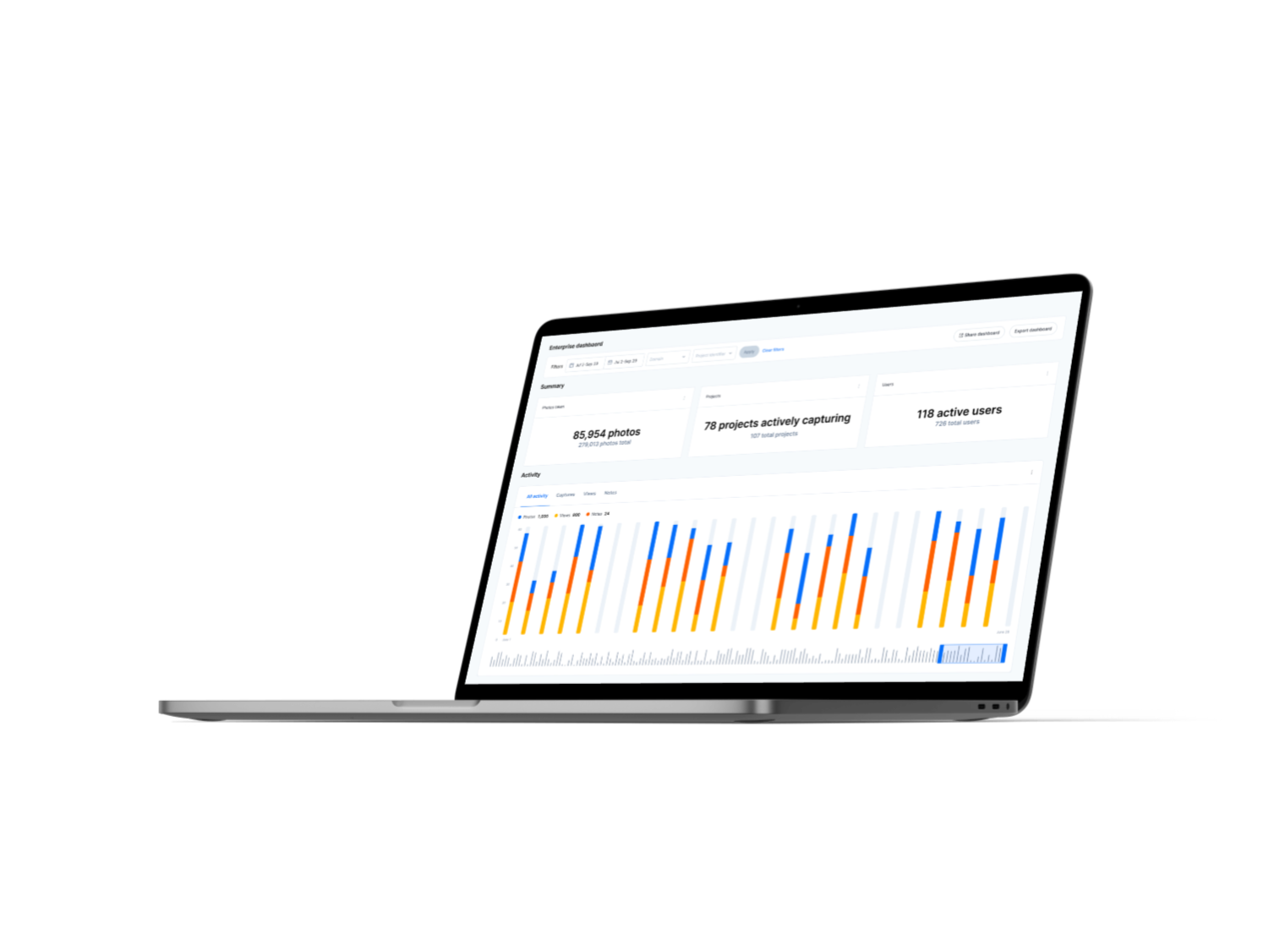
Enterprise & project dashboards
Use DroneDeploy's Enterprise Dashboard to see how frequently, and where, your interior images are being captured and viewed on projects across the company.
Automated reports
Progress Media, stockpile, and more
Automate reporting from DroneDeploy to send to external stakeholders. You can adjust both the interval of reporting and the people the data gets sent to.
Robotics
Ground robots are an increasingly popular tool for reality capture on construction sites. With DroneDeploy Robotics, you can:
Capture high-res images of building interiors
Carry multiple sensors (LiDAR, 360, PTZ)
Automate data capture missions 24/7
Upload data to the cloud for analysis
Track changes in buildings over time
Compare point cloud data with BIMs
Robots can capture LiDAR approximately 16x faster than terrestrial scanning. This can have a major impact on inspection times. For example, Turner Construction is using DroneDeploy and Boston Dynamics' Spot to cut site inspection times by 95%.