Within striking distance: risks and consequences of manual utility mapping (and how drones can help)
Building up starts by looking down at the underground utilities that run below your job site. Which means any construction project inevitably brings your crew into close proximity with a dangerous subterranean environment: tangles of fiber optic lines, water mains operating at over a hundred psi, high-wattage copper electricity cables, and cross-bore setups intersecting natural gas lines with sewage pipes.
Striking any of these subsurface utilities should be avoided at all costs. It can turn a trench into a pool, or knock out the internet of an entire neighborhood. It can bring the dread of calling the city supervisor to inform her you just hit a gas main adjacent to an elementary school. Or, worse, receiving a call from the hospital letting you know one of your crew was just admitted after a trench collapsed.
Calculating the costs of underground utility strikes:
→ An underground utility line is damaged once every nine minutes.
→ The average utility strike costs upwards of $50k in damages, totalling $61 billion a year in waste.
→ A subsurface utility strike occurs every 62 seconds, leading to over 2,000 injuries and 400 deaths yearly.
But there’s a better way:
→ Digitizing inspections with drone technology can improve accuracy by up to 90%, while cutting time spent on documentation by 50%, and significantly reducing the risk of injury, death and construction waste.
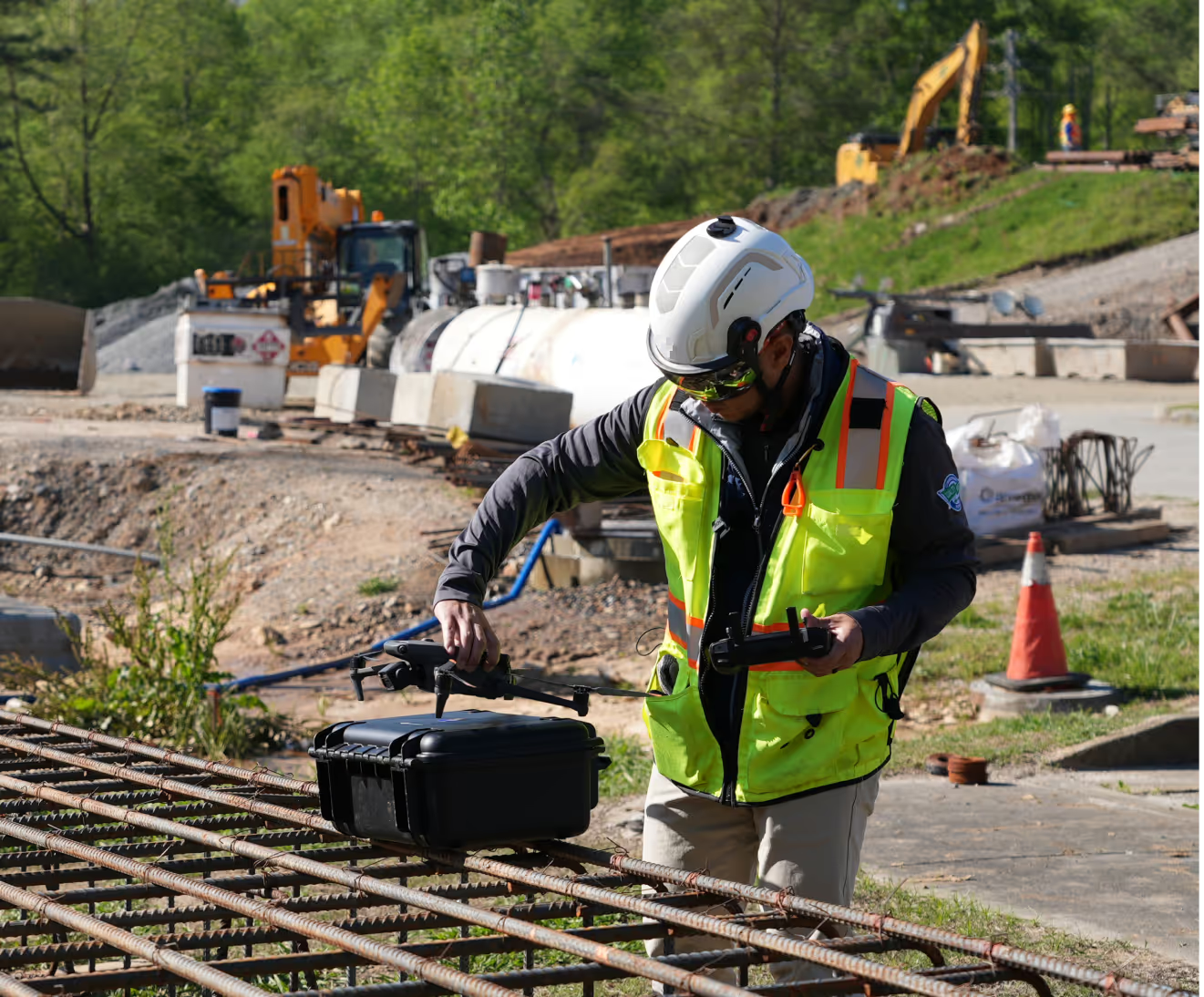
While there can be several factors at play during a utility strike, they can often be attributed to fragmented data coming from manual surveys. Let’s get into why this is an inferior way to survey and inspect underground utilities.
The Downsides of Manual Underground Utility Mapping
1. They’re incomplete representations of underground infrastructure and don't provide accurate mapping
When handing a project over to a site’s owner, you’re handing over more than plans and progress. You’re delivering peace of mind. It’s why having clear and accurate documentation is critical for not only the success of your current project, but your future relationship with the owner.
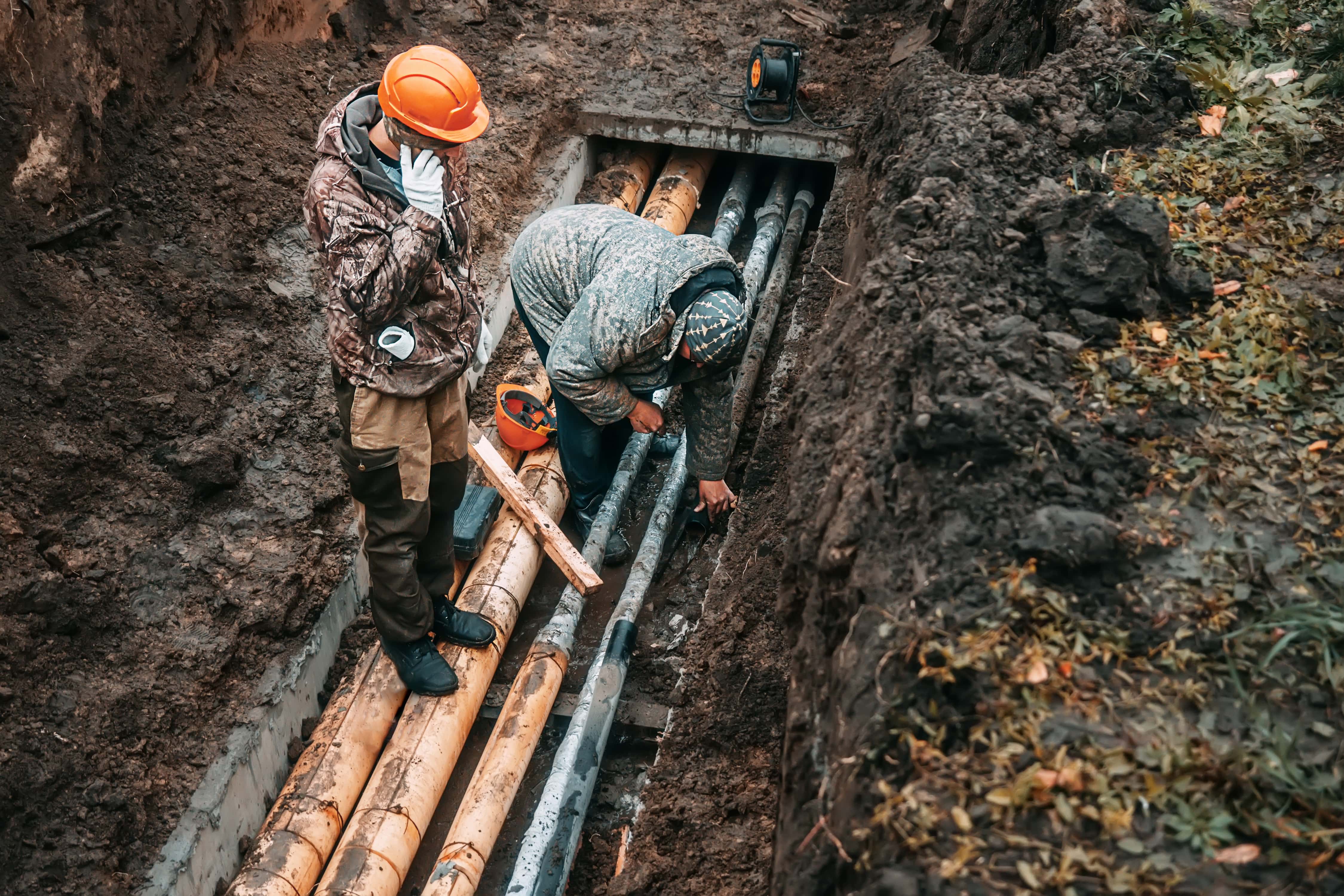
Manual surveys may miss critical location data, which increases the chances of a utility strike. It’s why, without comprehensive documentation of your site’s subsurface utilities, you run the risk of handing a blind spot over to your owner. Which can lead to a huge financial burden – everything from contractor claims, revised permitting submissions, project redesign, even litigation.

The manual way: Two months after you hand over your job, you get a call from the property owner shouting over a geysering water main about how your team gave them faulty depth.

Or with drones, you capture a time-lapse sequence that fully documents the project's progress, so you can demonstrate how the project evolved during handoff, verify that milestones were met and confirm locations of known utilities.
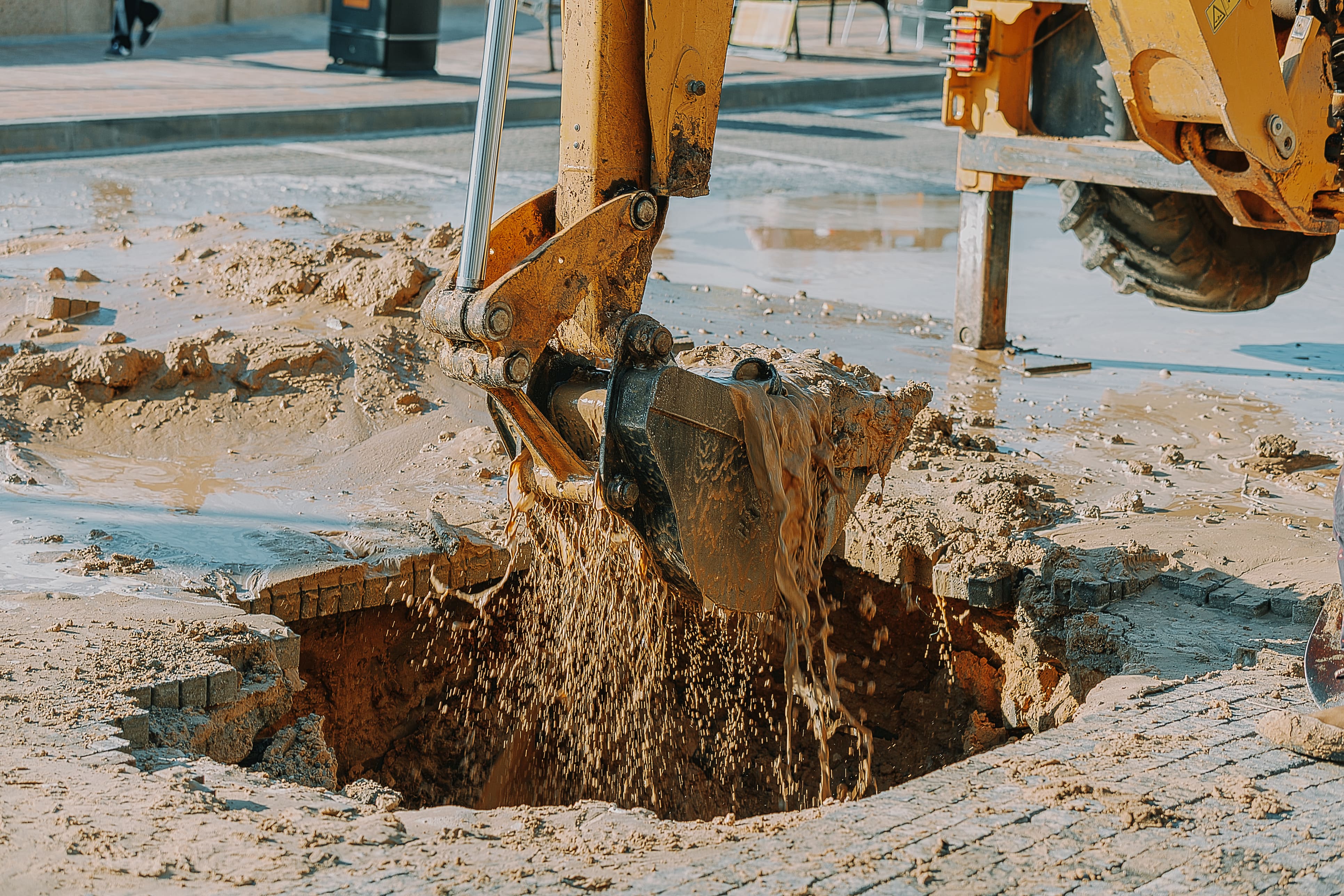
2. They’re dangerous and can lead to avoidable injuries
Thorough surveying is as much about understanding a utility’s environment as measuring its physical location. So when your only way of knowing your utilities is walking the site with a line locator, you’re missing several variables that can lead to ambiguous readings – particularly from nonmetallic materials like PVC conduits and polyethylene tubing for natural gas.
And when working on site, ambiguity can lead to an ambulance ride, as your crew runs the risk of arc flash injuries from disturbing an unseen electrical circuit or inhaling harmful vapors coming from a broken gas line.

The manual way: After getting a call from the hospital to inform you one of your crew members was admitted after being burned by an arc flash while excavating near a power line, you have to make a call to your crew member’s emergency contact to explain what went wrong.

Or you fly a drone that can capture manholes, electrical vaults and access points with high-resolution photogrammetry. Armed with this data, you can now correlate surface features with known utility maps, then deduce the presence and paths of underground electrical cables – all without ever stepping foot into a trench.
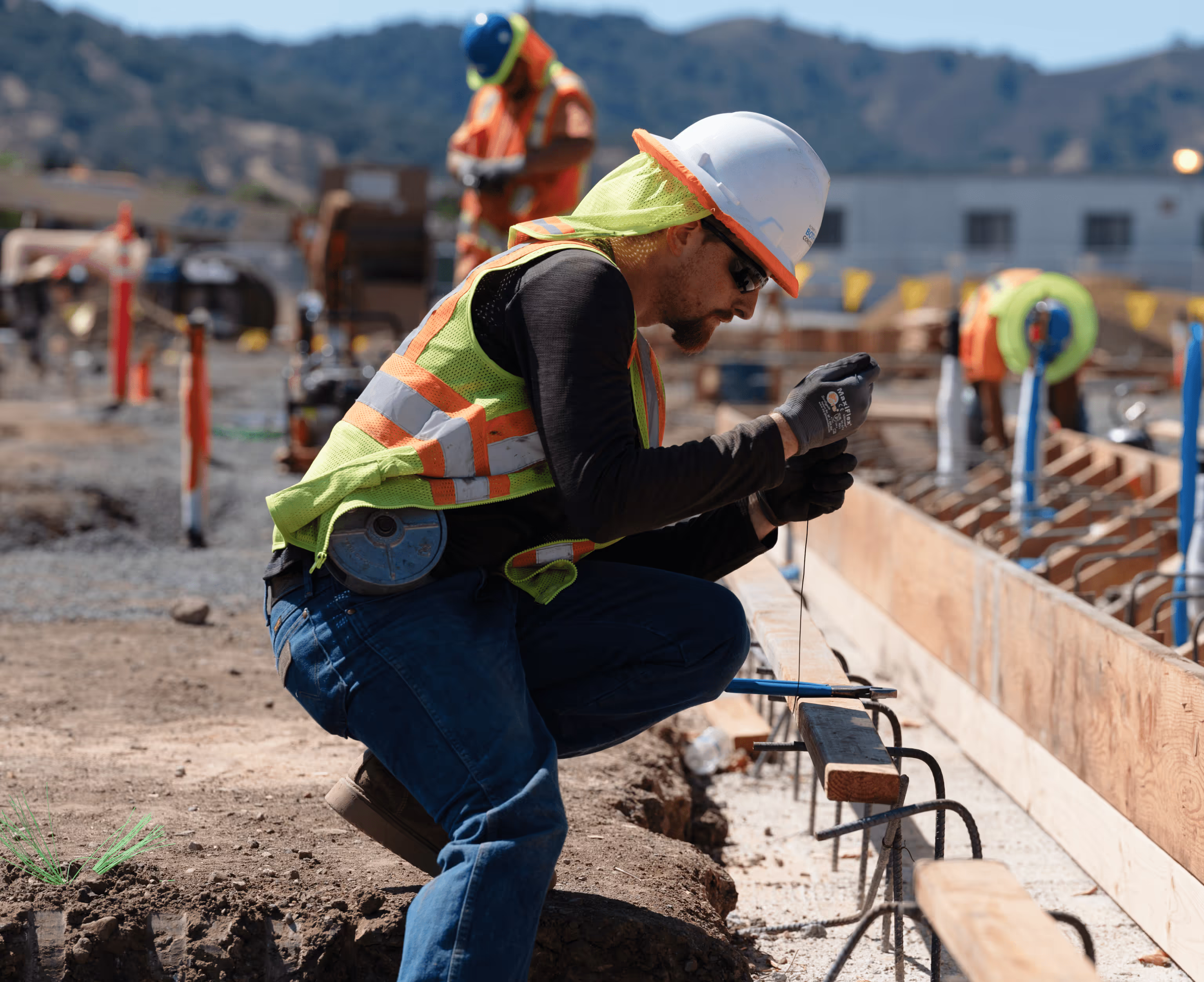
3. Quality Control: Manual mapping is inconsistent
Digging underground requires extensive coordination. You have to get the permit, close the road, prepare the site, dig the trench, do the work and then re-fill the hole. Each step along the way requires comprehensive – and cumbersome – documentation.
Doing all this manually not only eats up your team’s resources, it produces multiple sources of truth floating around one jobsite. And when teams lack a single source of truth about the location of subsurface utilities, it makes it near impossible to achieve consensus on critical decisions – for instance, creating avoidance zones for excavators and other heavy equipment.

The manual way: After completing the installation of a sewer system, you fill in the trench. Problem is, no one told the dozer operator about the location of this new system. Which means he runs over your sewer line, cracking the pipe.
Now you have to rip up pavement again, dig up the cracked pipe, slap on a new one, then refill the trench once more. And that’s the optimistic scenario: now imagine you don’t know the pipe’s cracked until the owner sees sewage leak up through freshly-laid asphalt.

Or with drones, you canvas areas where underground sewage mains are being installed. Now you can validate your utility locations and ensure avoidance zones are in place for every pipe that’s set.
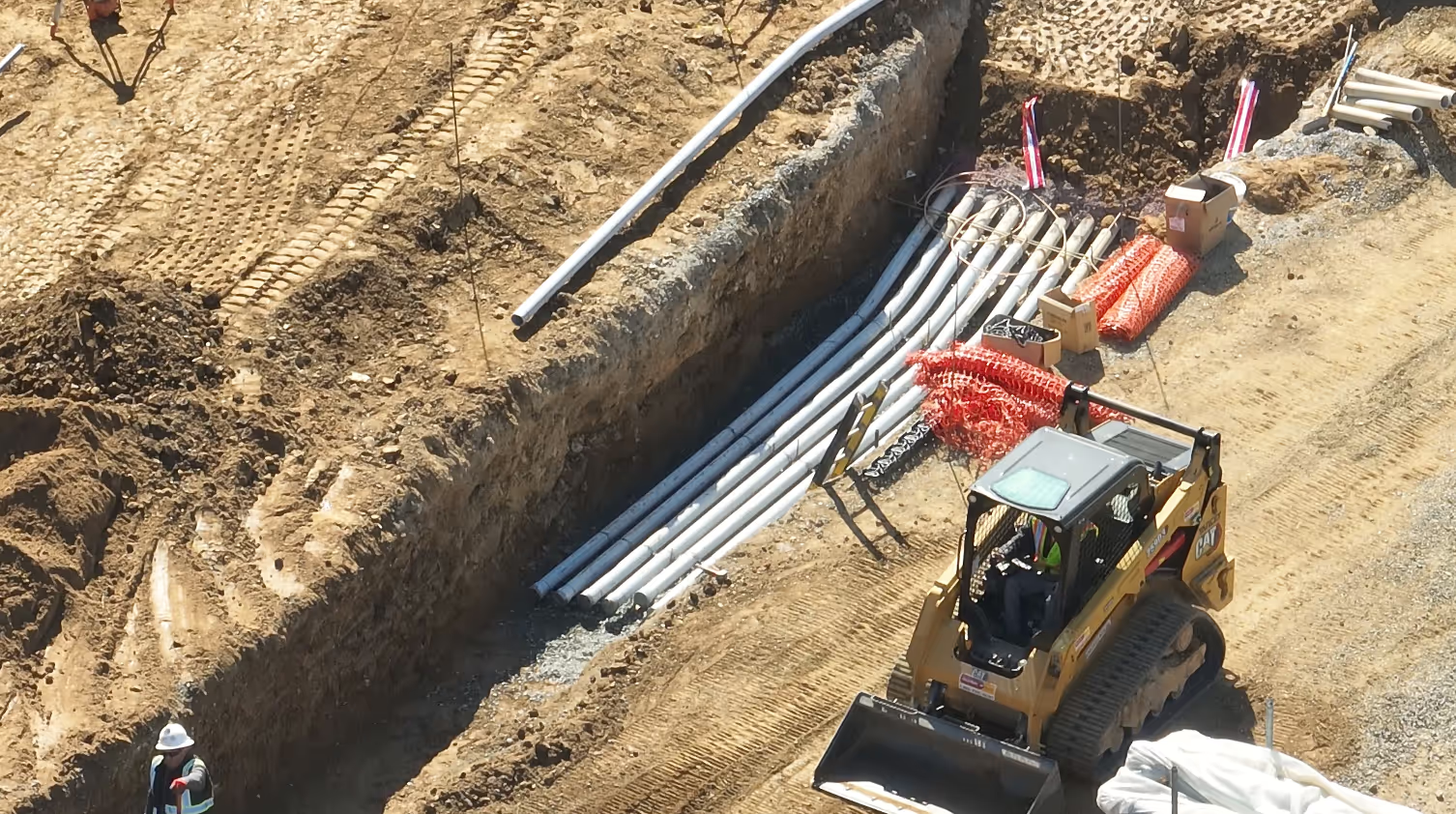
4. Underground mapping the manual way is inefficient
Like the infrastructure in which they document, paper surveys and inspection reports can deteriorate over the years from things like coffee stains, grease smudges and sunlight exposure. What’s more, finding paper documentation is a task in and of itself – think of all the hours spent canvassing the corporate office for physical copies either wedged in file cabinets or rolled up with 10 other utility drawings in a blueprint tube.
Then there’s the technical obsolescence of paper: its data is static, it lacks a search function, and sharing it is a huge chore – be prepared to either hover over your paper schematic with your smartphone’s camera, or drive the tube over to the site yourself.

The manual way
It’s time to handover the project to the owner, but your utility inspection reports were filed in the wrong project. Now the handover won’t include the inspection reports, unless someone somehow finds out which project they were misfiled in.

Or with drones, you’re able to instantly share your data with anyone in the world, so they can access your survey results wherever they are – and at a moment’s notice.
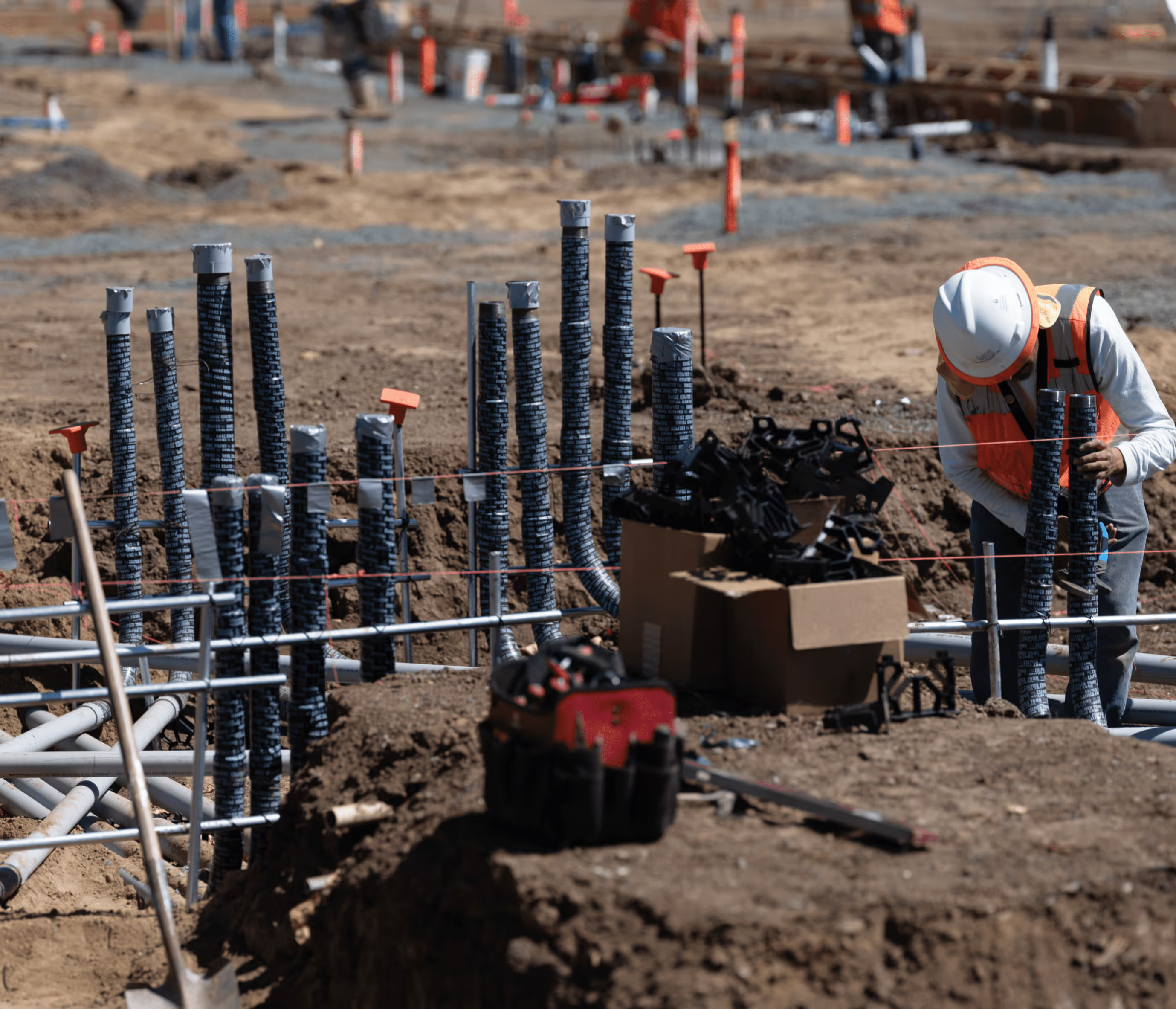
5. Manual mapping is infrequent, leading to a low level of accuracy
Because manual inspections are only performed occasionally (due to the time and resources involved), they can be outdated by the time they reach the contractor. This lag in information can result in costly delays and decisions made from stale, inaccurate data.

The manual way: You have a crew member survey your trench manually, but then a week of rain hits, changing the trench’s elevation. A line that was four feet from the surface is now two inches lower due to erosion.

With drones, you can take daily shots of the site to create a time-lapse sequence that shows the progression of the project over time so you can track soil erosion and stockpile quantities.
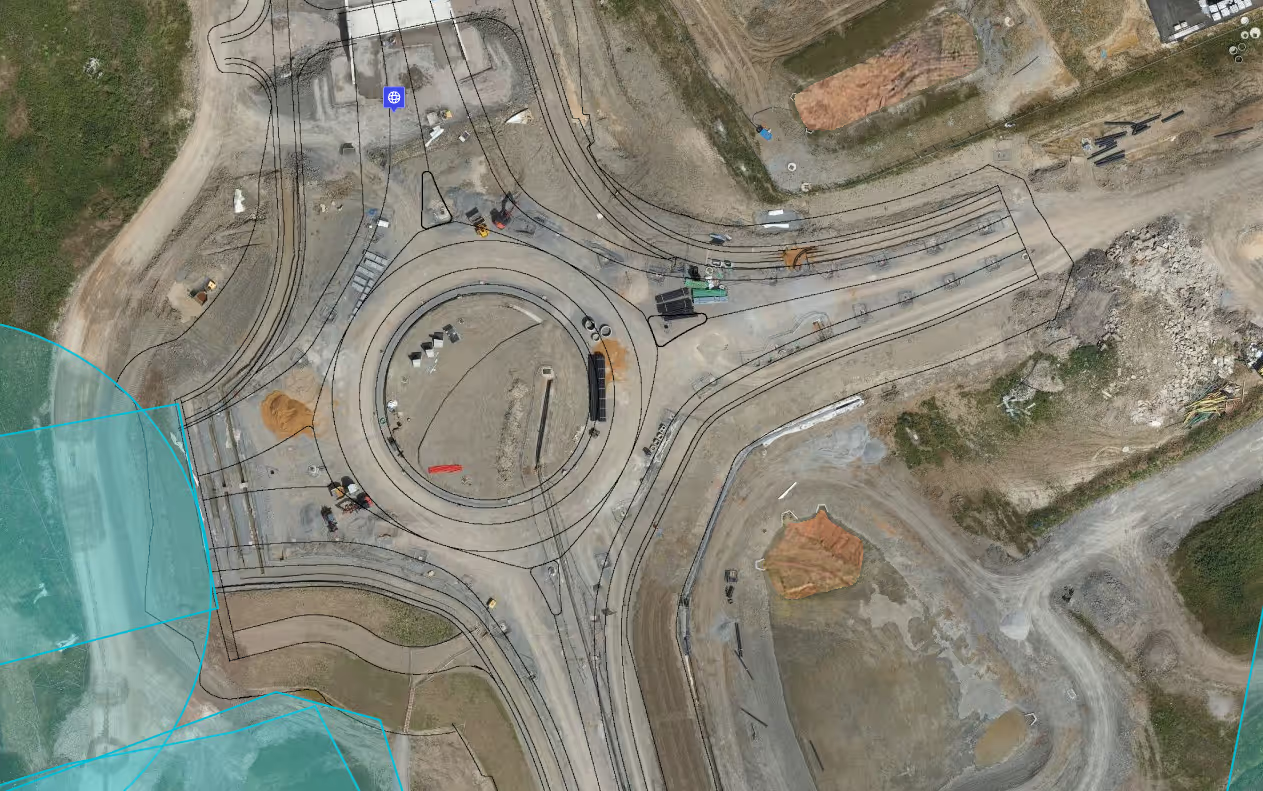
The better way forward for underground utility mapping
It’s imperative you know what lies underground, before breaking ground. While drones have been conventionally used for static photographs, they now have the ability to do so much more. Through a process called photogrammetry, high-accuracy GPS drones can now take hundreds of overlapping photos along an automated flight path, so you can create a complete model of reality that can be referenced against drawings, schematics and measurements.
In providing this complete model of reality, drones empower your team to survey subsurface utilities with confidence – everything from validating locations to spotting potential downstream issues and creating thorough documentation for handover.
Discover how Walsh Group is using reality capture to unlock a better way to inspect utilities. Watch the full video on DroneDeploy Insider
Stop breaking ground blind – and start making your utility surveys and inspections safer, simpler, and more accessible.
